Table of Contents
What Is In-house Order Fulfillment? The Ultimate Guide
Time: Dec 19,2024 Author: SFC Source: www.sendfromchina.com
In-house order fulfillment offers businesses a unique opportunity to take control of their supply chain and deliver an exceptional customer experience. But how does it work, and what makes it a smart choice for certain businesses? Our blog breaks down the process, advantages, challenges, and tips for optimizing your fulfillment operations.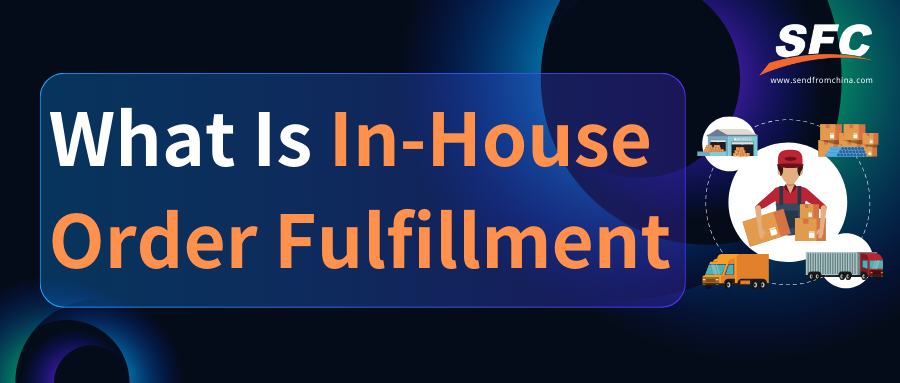
1. Understanding In-house Order Fulfillment
In-house order fulfillment refers to the process where a business manages every aspect of storing, packing, and shipping orders internally. Instead of outsourcing these operations to third-party logistics (3PL) providers, companies rely on their own resources, staff, and facilities to ensure that orders reach customers efficiently.Businesses often choose in-house order fulfillment for its potential to offer greater control over operations, improve customer satisfaction, and reduce costs for certain business models. It can suit startups, e-commerce brands, or companies aiming for a hands-on strategy in their supply chain.
2. What Are the Benefits of In-house Order Fulfillment
In-house fulfillment has several benefits, especially for small to medium-sized businesses looking to maintain control over their operations. Here are some reasons why companies choose this model:Greater Control Over Operations
Managing fulfillment internally allows businesses to maintain full oversight over the entire process. From inventory management to packaging and shipping, every step can be customized to align with your brand’s standards and values. The level of control helps ensure consistency in quality and service.Personalized Customer Experience
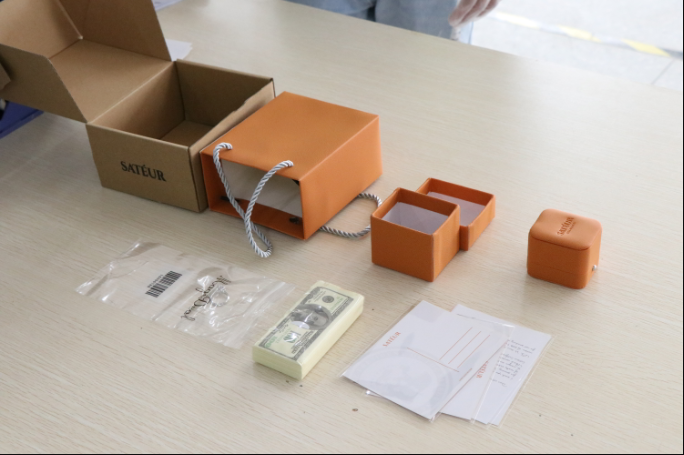
Cost Savings for Small Volumes
For companies with lower order volumes, in-house fulfillment can save costs by eliminating 3PL fees. Managing operations internally avoids the markup often associated with outsourced services.Faster Response Times
Having an on-site fulfillment team allows you to quickly address order changes, process returns, and resolve issues without relying on external providers. Agility is particularly valuable for time-sensitive promotions or unexpected order surges.Enhanced Data Security
Handling fulfillment internally minimizes the risk of sharing sensitive business data with third-party vendors, ensuring greater confidentiality.3. What Are the Challenges of In-house Order Fulfillment
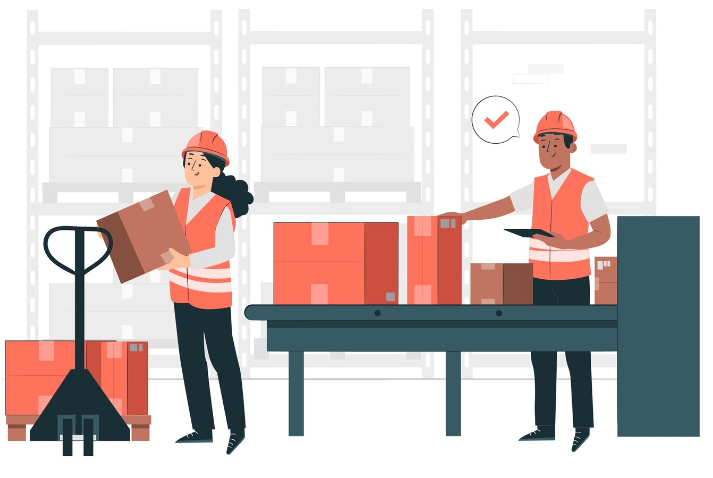
High Initial Costs
Setting up an in-house fulfillment operation requires significant investment in facilities, equipment, and technology. These upfront costs can be prohibitive for smaller businesses.Operational Complexity
Managing fulfillment involves juggling multiple tasks, including inventory tracking, order accuracy, and shipping logistics. Without robust systems in place, operations can quickly become overwhelming.Space Constraints
As your business grows, finding adequate storage space for inventory can become a challenge. Overcrowded warehouses lead to inefficiencies and errors.Resource Demands
In-house fulfillment requires dedicated staff and ongoing training. Additionally, businesses must allocate time and resources to manage the process effectively.Limited Scalability
Scaling an in-house operation to handle increased order volumes or expand into new markets can be difficult without substantial investment in infrastructure.4. How to Establish Your In-house Order Fulfillment
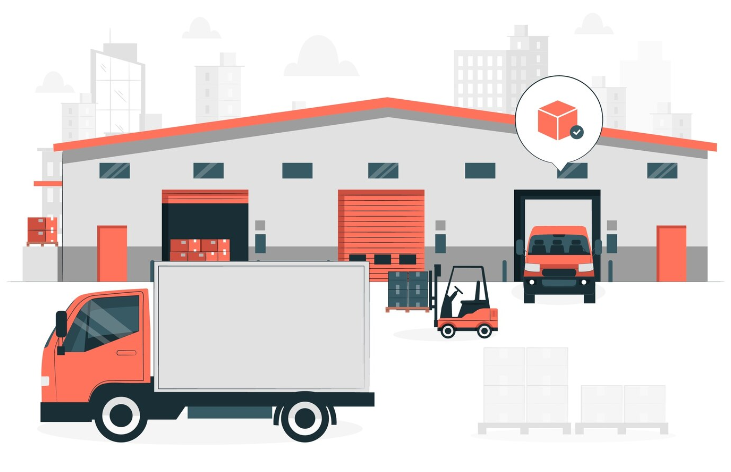
Create Your Storage Space
Begin by organizing your storage space to maximize efficiency. Choose a location that’s accessible and large enough to accommodate your inventory, with room for expansion. Designate specific zones for receiving, storage, picking, packing, and shipping. Use storage solutions like shelves, racks, and bins to make the best use of vertical and horizontal space. Implement clear labeling and categorization for quick item retrieval, and arrange products using systems like ABC analysis, where high-demand items are stored closer to picking stations.Make Your Fulfillment Strategy
Develop a strategy that outlines how orders will flow through your system, from receiving inventory to final shipment. Decide on picking methods (e.g., batch, wave, or zone picking) based on your order volume and product types. Establish a clear return process to handle customer exchanges or refunds. Additionally, determine key performance indicators (KPIs) like order accuracy, picking speed, and shipping times to evaluate your fulfillment effectiveness.Design Your Workflow
Map out each step of your order fulfillment process to ensure efficiency. Start with receiving inventory, then proceed to storage, order picking, packing, and finally shipping. Minimize unnecessary movements by creating logical paths and organizing workstations effectively. For example, place frequently picked items close to packing stations and use conveyor belts to transport products between zones. Incorporate technology like warehouse management system (WMS) to manage inventory levels, track orders, and guide picking.Build Your Team
Recruit and train a team skilled in various aspects of order fulfillment. Define roles such as inventory managers, pickers, packers, and shipping coordinators. Provide thorough training on safety protocols, equipment handling, and the use of technology. Encourage a culture of accountability and continuous improvement by setting performance goals and offering incentives for efficiency and accuracy. During peak seasons, hire temporary staff to handle increased demand.Set Up Shipping
Partner with reliable carriers to ensure timely and cost-effective delivery. Negotiate contracts to secure competitive rates and set up systems to automate label printing and shipping rate calculations. Offer customers multiple shipping options (e.g., standard, express) to enhance their experience. Use shipping software to integrate with your order management system for seamless label generation, tracking, and communication with carriers.Prioritize Customer Experience
Offer features that enhance the customer experience, such as real-time tracking, fast shipping options, and eco-friendly packaging. Ensure your packaging is secure and visually appealing to leave a positive impression. An efficient return and exchange process also contributes to customer satisfaction.Establish Clear Communication Channels
Set up clear communication protocols among your team and with customers. Internally, use systems that allow for quick updates on stock levels, order status, or workflow adjustments. Externally, provide customers with order confirmation emails, shipment tracking updates, and a hassle-free way to contact support for inquiries or issues.Evaluate Third-Party Partnerships
Even with in-house fulfillment, some aspects might benefit from outsourcing. For example, you could partner with a logistics provider for international shipments or a specialized firm for handling returns. These partnerships can complement your in-house operations and enhance your overall efficiency.5. How to Optimize Your In-house Order Fulfillment Process
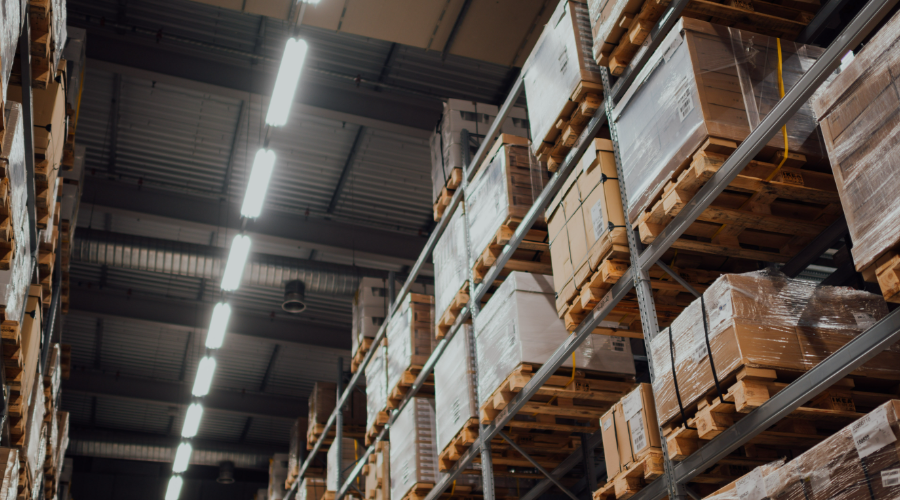
Warehouse Layout
Start by organizing your warehouse layout to maximize productivity. A well-structured warehouse separates receiving, storage, picking, packing, and shipping areas to eliminate clutter and confusion. Employ systematic storage practices like the ABC analysis, where frequently picked items are stored closest to packing stations, and ensure shelves and bins are clearly labeled for quick identification. This minimizes the time spent locating products.Automation
Automation plays a crucial role in streamlining operations. Invest in inventory management software to track stock levels, predict reorder points, and prevent overstocking or stockouts. Barcode scanning systems speed up picking and packing while reducing errors. At packing stations, tools like automatic tape dispensers and label printers can significantly cut down processing time. For picking orders, consider technologies like mobile apps that provide optimized routes for workers.Inventory Management
Inventory management is another critical aspect. Implement regular cycle counting instead of full warehouse shutdowns to keep inventory records accurate. Ensure stock levels are updated in real time to avoid overselling or delays in fulfilling customer orders. It not only improves operational efficiency but also builds customer trust by ensuring the products they order are available and shipped promptly.Employee Productivity
Employee productivity can be enhanced through proper training and incentives. Teach your staff best practices for picking, packing, and shipping to reduce errors and speed up processes. Providing ergonomically designed workstations minimizes fatigue and boosts morale, while performance-based rewards encourage efficiency. During peak seasons, hiring temporary workers can help manage the increased workload without overburdening your permanent staff.Reducing Shipping Costs
Reducing shipping costs is another vital consideration. Partner with multiple carriers to negotiate favorable rates and identify the best shipping zones for your key markets. Use lightweight, durable packaging to reduce shipping weights and costs. Standardizing packaging materials also minimizes decision-making time during packing, ensuring faster order processing. Additionally, offering eco-friendly packaging options not only appeals to environmentally conscious customers but can also help reduce waste and costs in the long term.6. In-house Order Fulfillment vs Outsourcing Fulfillment
The decision between in-house fulfillment and outsourcing depends on the size, goals, and budget of your business. Here’s a quick comparison: In-house Fulfillment |
Outsourced Fulfillment | |
Control |
Full control over processes | Limited control (handled by 3PL) |
Costs |
Cost-effective for low order volumes | Better for high order volumes (economies of scale) |
Scalability |
Limited scalability without major investments | Easily scalable with third-party resources |
Customer Experience |
Personalized branding and experience possible | Less personalization, depending on the 3PL |
Labor & Time |
Requires in-house staff and management | Saves time and reduces labor requirements |
When to Choose In-House Fulfillment:
- You’re a small to medium business with manageable order volumes.- You want to maintain control over packaging and shipping processes.
- Personalized branding and customer experience are priorities.
When to Outsource:
- You’re scaling rapidly and need help managing high order volumes.- You want to save time and focus on business growth.
- Cost-efficiency and expertise are critical factors.
7. Is In-House Fulfillment Right for You?
To determine if in-house fulfillment is right for your company, ask yourself these questions:- What’s my order volume? If you handle a small number of orders daily, in-house fulfillment could be manageable.
- Do I have the time and resources? Can you dedicate the space, staff, and systems needed to manage fulfillment?
- Is branding a priority? If personalized packaging is essential, in-house fulfillment is ideal.
- What’s my long-term growth plan? If you expect to scale quickly, you may need to consider outsourcing.
8. Conclusion
In-house order fulfillment gives businesses full control over their operations, allowing for greater flexibility and personalized customer experiences. While it’s ideal for small to medium-sized businesses, scaling may require significant investments in space, technology, and labor.9. FAQs
1. What businesses benefit most from in-house fulfillment?
Small to medium-sized businesses with low to moderate order volumes often benefit the most.2. How much space do I need for in-house fulfillment?
The space needed depends on your inventory size. Small businesses can start with a spare room or garage, but larger businesses may need warehouse space.3. Can I combine in-house fulfillment with outsourcing?
Yes! Some businesses manage high-value or personalized orders in-house while outsourcing bulk or international orders.
Copyright statement: The copyright of this article belongs to the original author. Please indicate the source for reprinting.
Previous Post
What Is Blind Shipping? Everything You Need to Know
Next Post
TAGS
Hot Research
Get a Custom China Fulfillment Solution with FREE Storage for 30 Days
Want to know about our services, fees or receive a custom quote?
Please fill out the form on the right and we will get back to you within a business day.
The more information you provide, the better our initial response
will be.