Table of Contents
2024 Warehouse Management Guide
Time: Jan 19,2024 Author: SFC Source: www.sendfromchina.com
Learn what warehouse management is and how to improve warehouse management efficiency.
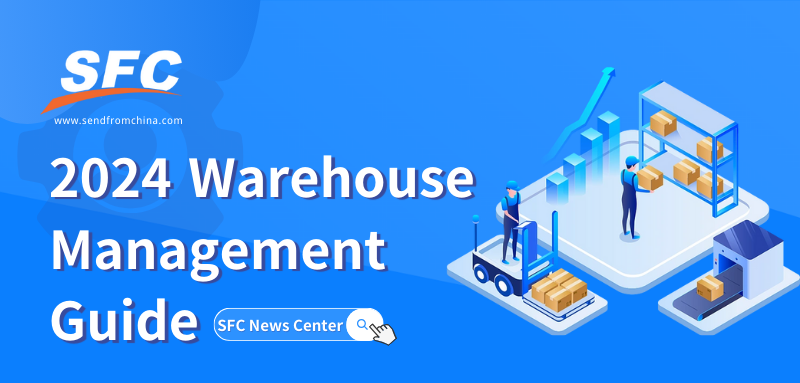
1. What Is Warehouse Management
Effective warehouse management ensures that goods are stored safely and efficiently, and are easily retrievable when needed. This process is essential for maintaining inventory accuracy, optimizing storage space, and ensuring timely order fulfillment. A well-managed warehouse can significantly contribute to the overall efficiency of the supply chain, reducing costs and improving customer satisfaction.
2. Why You Need Warehouse Management
Firstly, effective warehouse management is crucial for maintaining accurate inventory levels. Knowing exactly what is in the warehouse, where it is located, and how much stock is available is vital for fulfilling customer orders accurately and promptly. Poor inventory management can lead to issues such as overstocking, which ties up capital in unsold goods, or understocking, which leads to stockouts and missed sales opportunities. Efficient warehouse management ensures that a business can respond quickly to customer demands, maintain optimal inventory levels, and reduce holding costs, thus improving the overall financial health of the company.
Secondly, warehouse management plays a critical role in optimizing operations and improving efficiency. A well-organized warehouse with efficient processes can significantly reduce the time and effort required to store, locate, and move goods. This efficiency minimizes labor costs and enhances productivity. For instance, an efficient picking process ensures that orders are processed quickly, reducing the lead time from order to delivery. In addition, effective warehouse management can help in maximizing the use of space, which is particularly important in warehouses where space is a limiting factor. By strategically organizing products and utilizing modern storage solutions, businesses can make the most of their available space, potentially avoiding the need for costly warehouse expansions.
Finally, warehouse management is vital for ensuring customer satisfaction and maintaining a competitive edge. In today's fast-paced market, customers expect quick and accurate order fulfillment. Efficient warehouse operations directly impact the speed and accuracy of order processing, which in turn affects customer satisfaction. Moreover, as e-commerce continues to grow, the ability to manage returns efficiently — a process known as reverse logistics — becomes increasingly important. Effective warehouse management also helps in maintaining the quality of goods, as proper storage and handling reduce the likelihood of damage.
3. What Is Warehouse Management System
One of the key functions of a WMS is inventory management. The system provides real-time visibility into inventory levels, locations, and movements within the warehouse. This capability is crucial for maintaining accurate stock records, preventing overstocking or stockouts, and enabling just-in-time inventory practices. A WMS can also optimize warehouse space by efficiently organizing goods based on various factors like size, weight, and frequency of access. Additionally, the system can streamline the picking and packing processes, reducing errors and speeding up order fulfillment. This efficiency is particularly vital in today's fast-paced, e-commerce-driven market where quick turnaround times are essential.
Modern WMSs are highly sophisticated and can integrate with other supply chain management systems, such as Transportation Management Systems (TMS) and Enterprise Resource Planning (ERP) systems, providing a comprehensive view of the supply chain. They often utilize technologies like barcode scanning, RFID tagging, and automated guided vehicles (AGVs) to facilitate the tracking and movement of goods.
Advanced systems may also employ artificial intelligence and machine learning algorithms to predict inventory needs, optimize routes within the warehouse, and enhance decision-making processes. By providing detailed analytics and reporting, a WMS can also assist management in identifying trends, bottlenecks, and opportunities for further optimization. In essence, a Warehouse Management System is a vital tool for businesses looking to enhance their logistics efficiency, improve inventory accuracy, and boost customer satisfaction through faster and more reliable order fulfillment.
4. What Are the Processes of Warehouse Management
Receiving and Unloading:
Put-Away and Storage:
Inventory Management:
Order Picking:
Packing:
Dispatching and Shipping:
Returns Processing (Reverse Logistics):
Quality Control:
5. How to Improve Warehouse Management
5.1 Optimize Warehouse Layout
5.2 Utilizing Order Picking System
5.3 Warehouse Automation
This consistent operational speed ensures a steady flow of goods, leading to quicker processing times for receiving, storing, picking, and shipping. By automating repetitive and time-consuming tasks, warehouses can handle larger volumes of goods more efficiently, which is particularly beneficial during peak periods or seasonal surges in demand.
5.4 Measure Warehouse Performance
Regular monitoring of these metrics helps in identifying trends, pinpointing inefficiencies, and understanding the impact of changes made within the warehouse. Without measuring performance, it would be challenging to determine whether any changes or investments are yielding positive results.
5.5 Outsourcing to a 3PL (Third-party Logistics) Company
They possess the necessary infrastructure, technology, and systems to manage warehouse operations efficiently. By outsourcing, businesses can leverage this expertise without the need to develop it in-house, which can be particularly advantageous for companies whose core competencies lie outside of logistics. A 3PL provider can implement efficient warehouse processes, manage inventory effectively, and optimize order fulfillment operations, all of which contribute to enhanced warehouse efficiency.
6. FAQs About Warehouse Management
1. How is AI impacting warehouse management in 2024?
2. What are some effective ways to overcome space constraints in warehouses?
3. How important is sustainability in modern warehouse management?
4. What role does employee training play in warehouse management?
5. How can warehouses prepare for future challenges?

Copyright statement: The copyright of this article belongs to the original author. Please indicate the source for reprinting.
Previous Post
Why Is Shipping So Expensive 2024
Next Post
3PL Fulfillment: What Are The Role Of Third-party Logistics in 2024
TAGS
Hot Research
Get a Custom China Fulfillment Solution with FREE Storage for 30 Days
Want to know about our services, fees or receive a custom quote?
Please fill out the form on the right and we will get back to you within a business day.
The more information you provide, the better our initial response
will be.