Table of Contents
8 Most Common Shipping Problems and Solutions
Time: Oct 29,2024 Author: SFC Source: www.sendfromchina.com
Shipping plays a critical role in any business’s success, yet common shipping problems—like delayed shipments, lost packages, and high shipping costs—can disrupt even the most efficient operations. For businesses, these issues lead to customer dissatisfaction, increased expenses, and strained resources. Whether you’re navigating the complexities of international shipping or handling high volumes domestically, knowing how to tackle these issues is essential.In this guide, we cover the 8 most common shipping problems and solutions to help you streamline your shipping process, manage costs effectively, and ensure your customers receive their orders promptly and in perfect condition. Let’s dive into each problem and explore practical strategies to overcome them, so you can keep your logistics efficient and your customers happy.
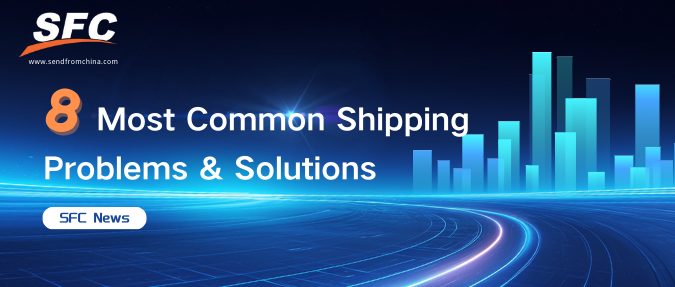
1. Delayed Shipment
Shipping delays are one of the most prevalent and frustrating issues faced in logistics. Delayed shipments occur due to various factors, such as weather conditions, supply chain disruptions, or incorrect documentation. These delays affect customer satisfaction and can lead to lost business, especially when time-sensitive goods are involved. Here’s how to manage and prevent shipping delays effectively.Identifying Causes of Delayed Shipments
A comprehensive understanding of the root causes of shipping delays is essential. These causes typically include:Weather Disruptions: Natural factors like storms, snow, or hurricanes.
Supply Chain Breakdowns: Sudden supply chain disruptions can halt entire delivery timelines.
Documentation Errors: Missing or incorrect paperwork can lead to customs or carrier delays.
Solutions for Preventing Shipping Delays
Real-Time Tracking Systems: Implement advanced tracking tools that provide real-time updates, allowing both the logistics team and customers to stay informed on shipment progress.Communication Protocols: Set up clear communication channels between suppliers, carriers, and customers to alert them promptly if delays occur.
Buffer Times: Establish a buffer period in your delivery timeline to accommodate unexpected delays, ensuring customer expectations are managed.
2. Lost or Misplaced Packages
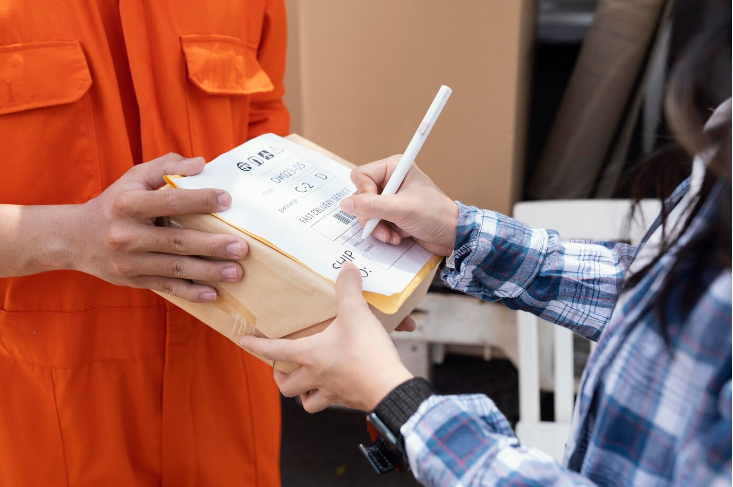
Understanding Causes of Lost Packages
Common causes of lost packages include:Inadequate Tracking: Packages that lack tracking systems can be harder to locate.
Labeling Errors: Misprinted labels lead to packages ending up in the wrong destinations.
Carrier Mishandling: High volumes and understaffing issues in warehouses can lead to misplacement.
Solutions to Minimize Lost Packages
Enhanced Tracking Systems: Use GPS tracking for high-value packages to monitor their location throughout the entire shipping journey.Label Verification: Implement scanning and verification processes to ensure all labels are correctly printed and affixed.
Customer-Centric Communication: Keep customers informed throughout the process, especially if any issue arises with their package. It builds trust and improves transparency.
3. Damaged Goods
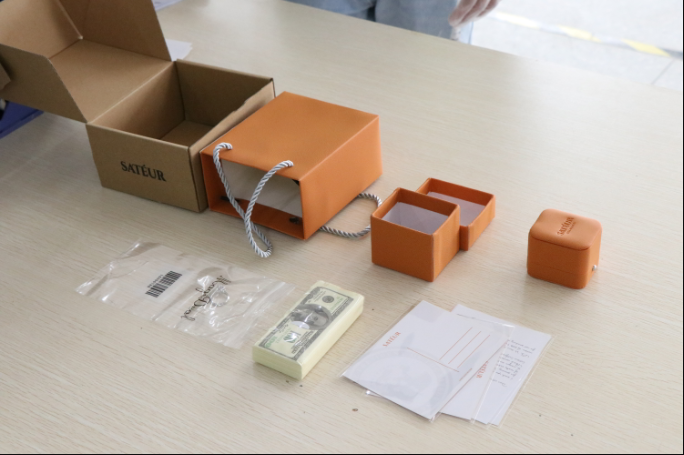
Causes of Damaged Goods
Damaged goods often result from:Insufficient Packaging: Poor packaging materials can’t protect items from impact or environmental factors.
Improper Handling: Mishandling in warehouses or during delivery can lead to breakage.
Environmental Exposure: Extreme temperatures or humidity can damage sensitive items.
Solutions to Prevent Damaged Goods
Optimize Packaging Materials: Use robust and appropriate packaging materials, like bubble wrap, padding, and durable boxes.Train Warehouse Staff: Implement strict handling protocols, including specific handling instructions for fragile goods.
Use Temperature-Controlled Shipping: For goods sensitive to temperature, use climate-controlled vehicles or packaging to maintain optimal conditions.
Quick Response for Damaged Goods
To reduce dissatisfaction, adopt a rapid-response strategy for customers who receive damaged items. It includes a simple return process, offering replacements, or issuing refunds swiftly.4. High Shipping Costs
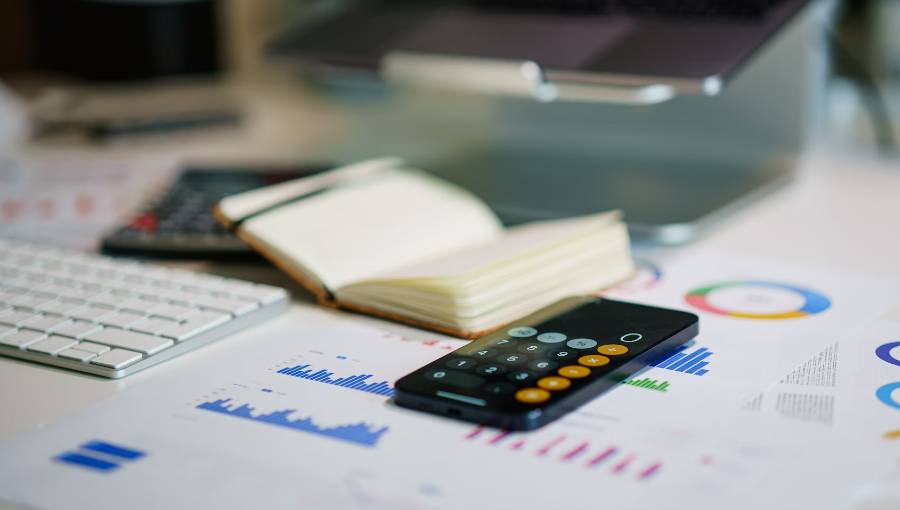
Causes of High Shipping Costs
Shipping expenses can spike due to:Fuel Surcharges: Increased fuel costs are directly passed on to shipping costs.
Overly Expensive Packaging: Heavy or large packaging materials increase dimensional weight charges.
International Tariffs: Cross-border shipping incurs additional fees, impacting cost-effectiveness.
Solutions for Reducing Shipping Costs
Negotiating Carrier Contracts: Regularly negotiate rates with multiple carriers to obtain competitive prices.Optimize Packaging Dimensions: Use packaging that is compact yet protective to reduce dimensional weight charges.
Leverage Automation for Cost Analysis: Automated tools can analyze shipping patterns, helping find the most cost-effective carrier for each shipment.
5. Customs Delays
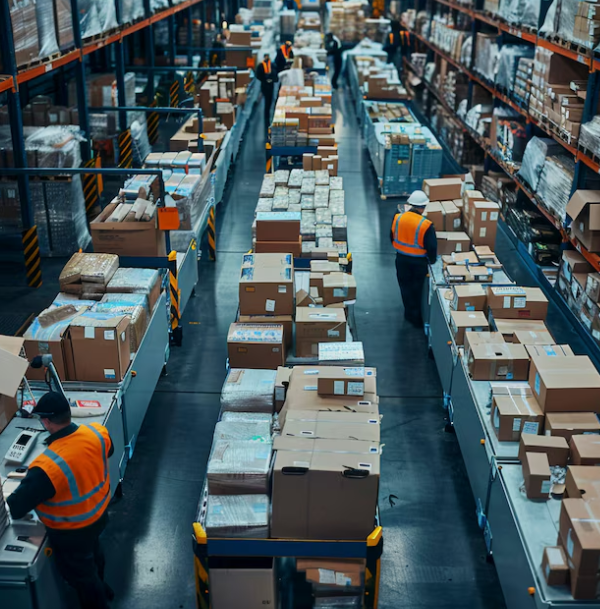
Common Causes of Customs Delays
Customs delays can be caused by:Incomplete Documentation: Missing or inaccurate documents like invoices, certificates, or permits.
Non-Compliance with Regulations: Items not meeting import/export standards face delays or even seizures.
High Volume Periods: Busy shipping seasons, like holidays, lead to congestion and longer clearance times.
Solutions to Avoid Customs Delays
Pre-Clearance Procedures: Prepare documents in advance and double-check for accuracy.Understanding Local Regulations: Stay updated on regulatory requirements for the countries you ship to and ensure compliance.
Partner with Customs Brokers: Customs brokers can expedite the process by navigating complex documentation and regulatory checks.
6. Incorrect Address Information
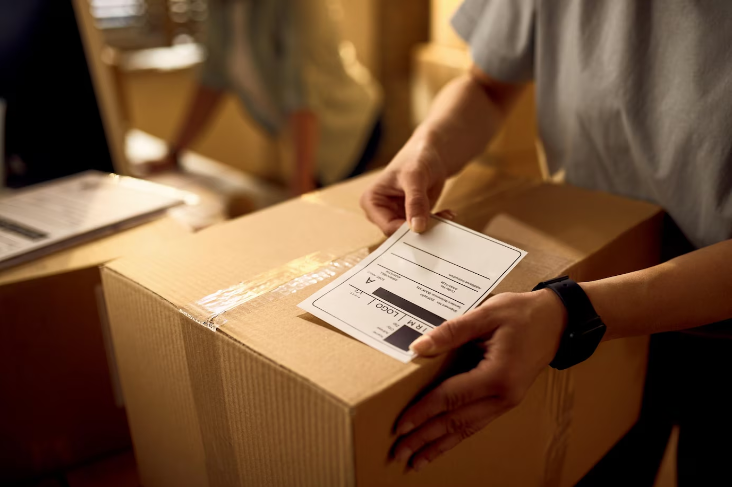
Common Causes of Address Errors
Address errors are usually due to:Manual Entry Mistakes: Incorrect or incomplete addresses entered during the order process.
Auto-Generated Errors: Address auto-completion features can sometimes produce inaccurate results.
Customer Input Errors: Customers may inadvertently enter incorrect details, especially in international addresses.
Solutions for Minimizing Address Errors
Automated Address Verification Tools: Integrate address verification software to catch and correct errors during order placement.Clear Input Forms: Simplify address fields on your website, especially for international addresses.
Proactive Communication with Customers: When an address issue is identified, reach out to the customer immediately to confirm or correct details.
Creating Address Correction Protocols
Have a process in place for handling incorrect addresses swiftly to avoid delays, like verifying addresses through customer service before shipping.7. Managing Returns Efficiently
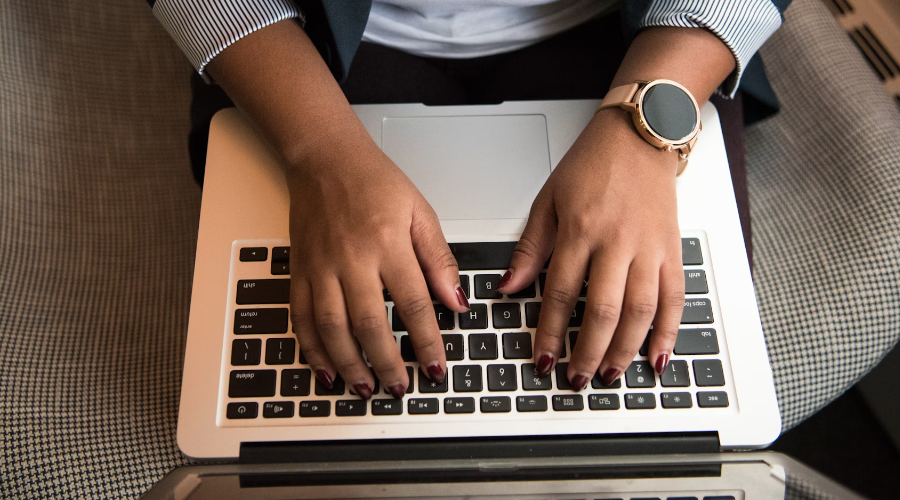
Reasons for Return Complexity
Return processes become challenging due to:Complex Return Policies: Confusing policies frustrate customers and increase support requests.
High Costs Associated with Returns: Shipping back returned items adds costs, impacting profit margins.
Lack of Automation in Processing Returns: Manual returns processing can be time-consuming and prone to errors.
Solutions for Streamlining Returns
Implement a Clear Return Policy: Establish transparent policies that detail how customers can initiate returns, deadlines, and conditions.Automate the Return Process: Use return management software to automate approval, tracking, and refund processes.
Offer Local Return Options: Partner with regional warehouses or service providers to simplify the return process, especially for international customers.
8. Customer Dissatisfaction Due to Delivery Issues
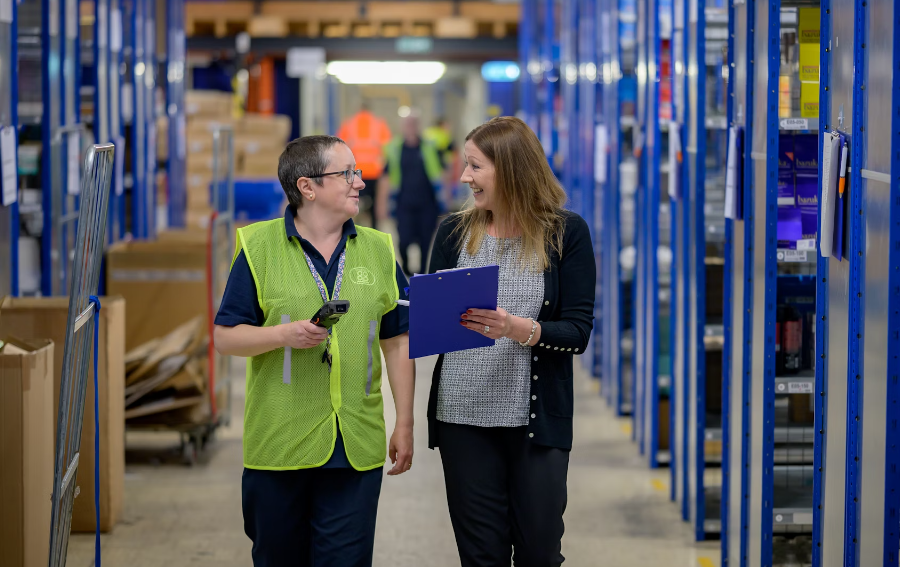
Common Causes of Dissatisfaction
Customer complaints often stem from:Delayed Deliveries: Missed delivery timelines are a leading cause of dissatisfaction.
Unclear Communication: Lack of updates on delivery status makes customers feel ignored.
Damaged or Lost Goods: Customers expect their packages to arrive intact and on time.
Solutions for Improving Delivery Satisfaction
Set Accurate Delivery Expectations: Be realistic about delivery timelines and communicate any potential delays as early as possible.Provide Tracking Information: Keep customers informed through tracking tools and proactive notifications.
Resolve Complaints Quickly: Have a dedicated customer support team to address any delivery issues immediately, whether it’s rerouting a package or issuing a refund.
9. FAQs
What can I do if my shipment is delayed?
First, check with the carrier for updates and estimated delivery. Often, delays are communicated via tracking tools. If the delay is prolonged, consider alternative shipment options or notify your customers to manage expectations.How can I reduce shipping costs without compromising quality?
Negotiate rates with multiple carriers, use dimensional weight pricing for packaging, and leverage automated tools to select the most cost-effective carrier for each shipment.Why are my packages getting damaged during delivery?
Packages can be damaged due to insufficient packaging or mishandling during transit. Use robust packaging materials, train staff on proper handling, and consider climate-controlled options for sensitive goods.How can I prevent lost packages?
Lost packages are often due to inadequate tracking and labeling issues. Implement GPS tracking for valuable shipments, and ensure labels are verified before shipping to minimize misplacement.What should I include in my customs documentation?
Include all required documentation, such as commercial invoices, packing lists, certificates of origin, and any permits specific to the items being shipped. Incomplete or incorrect paperwork is a common cause of customs delays.
Copyright statement: The copyright of this article belongs to the original author. Please indicate the source for reprinting.
Previous Post
Shipping from China to Mexico: A Comprehensive Guide
Next Post
How to Kickstart a Board Game: A Step-by-Step Guide for Creators
TAGS
Hot Research
Get a Custom China Fulfillment Solution with FREE Storage for 30 Days
Want to know about our services, fees or receive a custom quote?
Please fill out the form on the right and we will get back to you within a business day.
The more information you provide, the better our initial response
will be.