Table of Contents
What Is Warehouse Quality Control
Time: Mar 19,2025 Author: SFC Source: www.sendfromchina.com
Key Takeaways
- Warehouse quality control (QC) involves systematic checks to ensure products meet standards before reaching customers.- Effective QC reduces errors, boosts customer trust, and saves costs.
- Processes include inspections, inventory audits, and real-time tracking.
- Partnering with QC-focused warehouses like SFC mitigates risks and enhances brand reputation.
1. What Is Quality Control in Warehouse
Warehouse quality control is the process of monitoring and evaluating all aspects of warehouse operations to ensure they meet certain quality standards. In simple terms, it means ensuring that every product handled in the warehouse is in good condition, stored properly, and picked and packed accurately. According to industry experts, warehouse quality control involves setting up rules and procedures so that goods are handled safely and orders are fulfilled correctly, in good condition, and on time. It ensures all work is done according to your business’s standards and helps reduce errors, improve efficiency, and save moneyIn practice, quality control in warehousing covers each stage of the workflow. For instance, when new stock arrives, QC measures would include verifying the quantity received matches the packing list and checking the quality of items (looking for damage, defects, or wrong items). Similarly, before orders leave the warehouse, QC means confirming the right products are packed, in the correct quantities, with no damage, so that customers receive exactly what they ordered in perfect condition. Essentially, warehouse QC acts as a safeguard to catch and correct any issues before products reach the end customer. It not only keeps customers happy but also protects the seller’s brand reputation by ensuring only high-quality goods go out the door.
It’s worth noting that quality control (QC) is related to but slightly different from quality assurance (QA). QC is about inspecting and catching problems in products or processes (reactive checks), while QA is about setting up processes to prevent those problems in the first place (proactive management). In a warehouse context, QC might be the worker on the dock inspecting a shipment for damage, whereas QA would be the overall system or policy that ensures workers are trained and processes designed so that errors are less likely to happen at all. Both work hand-in-hand to maintain high standards in the warehouse.
2. Why Quality Control Matters in Warehouse
Quality control is crucial in warehousing because it directly impacts cost, warehouse efficiency, and customer satisfaction. A warehouse might seem like just a storage place, but how things are managed inside has a major effect on the customer experience and the business’s bottom line. Here are a few reasons why QC matters:Error Reduction and Cost Savings
Even a small error rate can be very costly. The average warehouse or distribution center has a picking error rate between 1% and 3%, meaning out of 100 orders, 1–3 may be wrong. That may sound small, but studies show a single order error (like sending the wrong item) can reduce that order’s profitability by as much as 13%. These errors add up through wasted shipping costs, re-shipping, handling returns, and losing the customer’s trust. By implementing strict quality control, warehouses catch mistakes (wrong item, wrong quantity, etc.) before they ship out. Fewer errors translate to immediate cost savings and higher profit margins.Customer Satisfaction and Brand Reputation
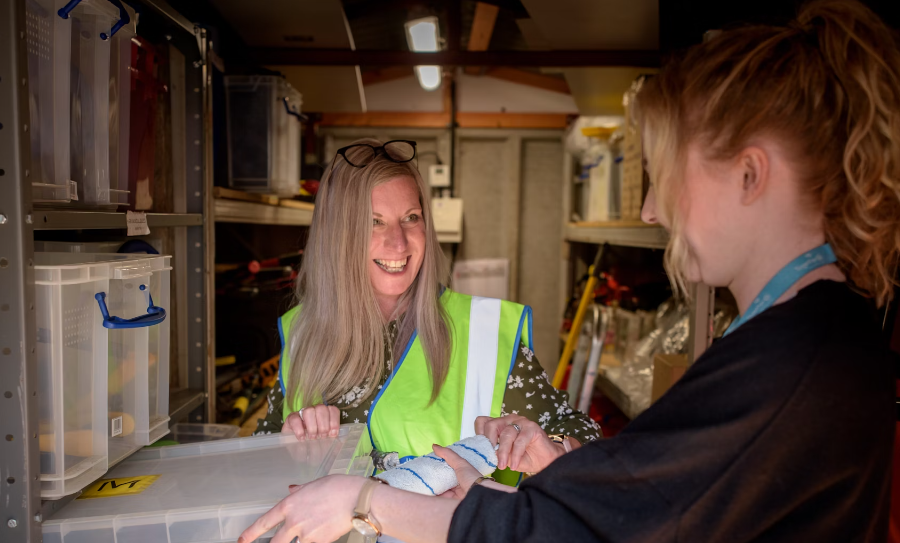
Efficiency and Waste Reduction
A well-controlled warehouse runs more smoothly. When quality control processes are in place, workers have clear checkpoints and standard procedures, which reduces confusion and delays. For example, checking inventory upon receiving prevents miscounts that could lead to stock discrepancies later. Verifying storage conditions (right temperature, no hazards) prevents spoilage or damage. All of this avoids waste – whether it’s wasted time searching for missing products or scrapping expired/damaged goods that weren’t noticed in time. Efficient QC ultimately means the warehouse can process orders faster with less rework. According to experts, quality control helps maintain specific standards and minimizes errors and waste, which eventually improves overall operational efficiency.Regulatory Compliance and Safety: In certain industries (food, pharmaceuticals, electronics), warehouses must meet safety and quality regulations. Quality control measures (like lot tracking, inspections, proper storage protocols) ensure that products remain compliant with health and safety standards while in storage, avoiding legal issues and ensuring end consumers are safe. Even in general retail, QC improves safety – employees are less likely to trip over improperly stored goods, and customers are less likely to receive unsafe products. So QC also matters from a risk management perspective.
3. What Warehouse Quality Control Does
Warehouse quality control encompasses a range of practices and checks throughout the warehousing process. Essentially, it’s what the warehouse team does to maintain quality at each step – from receiving goods to shipping orders. Here are the key activities that fall under warehouse QC:Incoming Goods Inspection
The QC process starts as soon as products arrive at the warehouse. The receiving team will inspect incoming shipments to verify that the quantity received matches the supplier’s packing list and purchase order, and that the quality is up to standard. They look for any damage that might have occurred in transit (e.g. crushed boxes, leaking containers) and check that the correct items were delivered (matching SKUs or product descriptions). If any defects or discrepancies are found, they can be addressed immediately – such as logging a damage report or refusing the delivery. The incoming inspection prevents storing defective stock or incorrect items. It’s much easier and cheaper to fix an issue at the receiving dock than after products are put away or shipped to a customer.Proper Storage and Handling
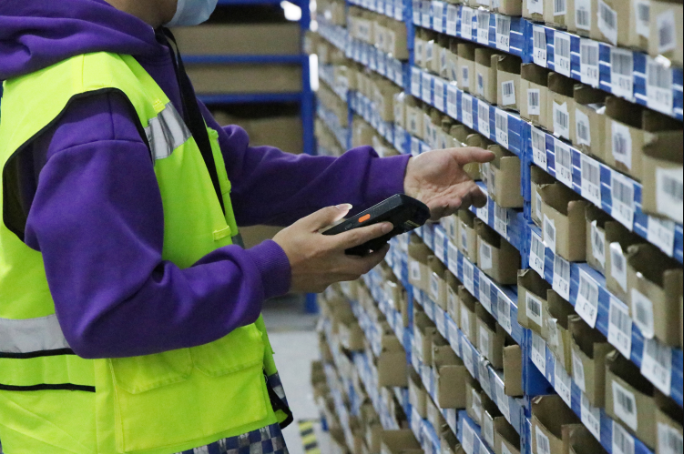
Inventory Monitoring and Audits
Regular inventory checks are another facet of warehouse QC, including cycle counting (periodically counting a subset of inventory) or full warehouse audits to ensure the physical stock matches the inventory records. Discrepancies might indicate an error like a misplaced item, a theft, or a counting mistake during receiving.By catching those through audits, the warehouse can correct inventory records and investigate the root cause. Inventory monitoring also involves watching for products that may expire or become obsolete – a quality-controlled warehouse will have processes to rotate stock (e.g., FIFO – first in, first out for perishable goods) so that older inventory ships out first and nothing expires on the shelf. Keeping accurate, up-to-date inventory with routine checks ensures that when an order comes in, the item is actually there and in good condition to ship.
Order Picking and Packing Checks
When it’s time to fulfill orders, quality control procedures kick in again. During picking, workers should double-check that they are selecting the correct item and the correct quantity for the order. Many warehouses use barcode scanners and order verification systems as part of QC – the picker scans the location or product barcode which confirms if it’s the right item. It significantly reduces human error (in fact, warehouses that implement barcode scanning and other technologies have achieved order accuracy rates of 99.9% or higher).After picking, during packing, the staff typically perform another check: matching the picked items against the packing slip or order invoice to ensure nothing is missing or extra. They also inspect items for any damage one more time and ensure they’re packaged securely so they won’t break in transit. The final QC step before sealing the box is crucial – it’s the last opportunity to catch a mistake or defect. Robust warehouses even have a “two-person rule” or systematic scan at pack-out: one person packs and another verifies, or the system forces a scan of each item in the box to confirm it’s the correct product.
Outbound Quality Inspection
Some operations include a final outbound QC, where packed orders (especially large shipments or high-value products) are audited randomly or at set intervals. For instance, a supervisor might double-check 1 out of every 100 packages to ensure it has the correct contents and is labeled properly. It adds an extra layer of confidence that the warehouse’s processes are working. Additionally, if an order is being prepared for a retail store or an important client, the warehouse might do a detailed quality checklist – confirming labeling, documentation, and palletization meet all requirements.Continuous Improvement and Feedback
Quality control is an ongoing cycle. A good warehouse QC system will also collect data on errors or issues found and use that to improve. For example, if inbound inspection often finds the same defect from a supplier, that information is relayed back to the supplier to fix their packaging or production. If picking errors are occurring in a certain area of the warehouse, maybe the layout needs improvement or the staff need more training in that section. Regular team meetings or QC reports help identify problem trends. Over time, these improvements mean fewer errors to catch in the first place. In short, the warehouse learns from any quality slip-ups and adapts to prevent them going forward.4. Why Business Should Choose Warehouses with Quality Control Services
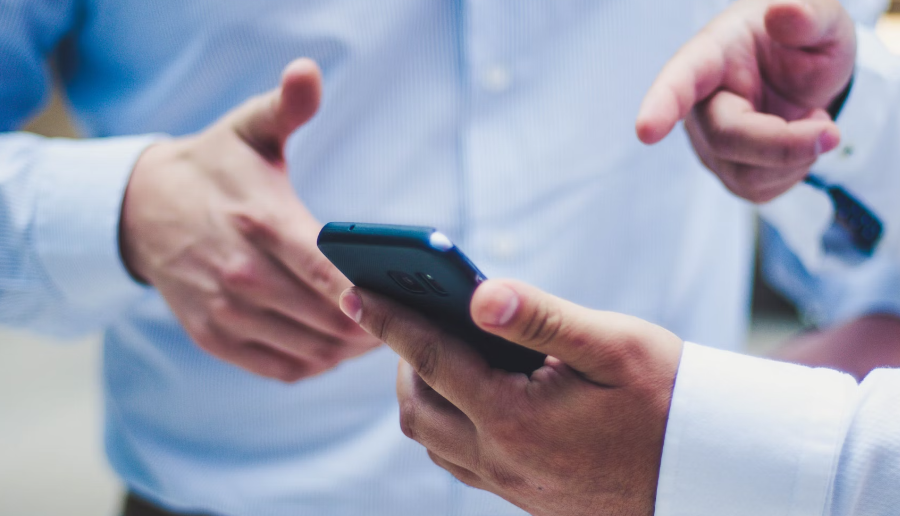
- Risk Mitigation: A third-party logistics (3PL) provider with QC shares liability for errors. If a shipment fails, they cover replacement costs—not your business.
- Scalability: Seasonal spikes? QC systems adapt. During peak holidays, warehouses like SFC deploy temporary staff trained in QC protocols to maintain standards.
- Tech Edge: Many QC-focused warehouses use tools you can’t afford in-house, like blockchain for traceability or IoT sensors for temperature monitoring.
- Reputation Shield: Consistent quality builds brand loyalty. A 2023 Gartner survey found that 68% of customers pay more for brands with reliable delivery.
5. How SFC Supports Better Warehouse Quality Control
SFC (SendFromChina) is a real-world example of a warehouse and order fulfillment provider that emphasizes strong quality control. For businesses shipping products from China to global markets, SFC offers end-to-end fulfillment with rigorous QC embedded in each step. Here’s how SFC supports better warehouse quality control and ensures high standards:
Inbound Quality Inspection
SFC performs thorough quality control checks as soon as your goods arrive at their warehouse. According to SFC, they “identify and address quantity or quality issues before [storage]”. In practice, this means if you ship products from your factory directly to an SFC warehouse, their team will count everything and examine product conditions upon receipt. Any discrepancy in quantity or any defect/damage in quality is flagged immediately.By doing this, SFC guarantees inventory accuracy and product quality from the start, which in turn reduces the risk of problems later like stock count errors or customer returns. For clients, this is invaluable – it’s like having a dedicated inspection team on the ground in China making sure only good stock goes into storage. (In fact, SFC often recommends sellers send goods to their warehouse directly from factories for this reason, so that any issues can be caught early.)
Product Labelling and Tracking
As part of their inbound process, SFC doesn’t just inspect but also labels each item with barcodes and tracking identifiers. They mention that each piece is labeled with a unique barcode and for valuable products they even assign separate tracking numbers. The level of item-level tracking is a form of quality control because it virtually eliminates mix-ups in the warehouse. With everything barcoded, SFC’s system can track every movement of each SKU, ensuring the right item is picked every time.The company states that this helps ensure “zero error in warehouse and picking”. While zero error is the ideal goal, SFC’s actual performance is impressive – they report an inventory accuracy higher than 99%, meaning their stock counts and records are almost always spot-on. Such accuracy is achieved through these diligent labeling and system controls.
Advanced Warehouse Management System (WMS)
SFC supports its QC with technology. They use an advanced WMS that keeps inventory data synced in real time and guides the warehouse operations. The system likely powers features like automated inventory updates upon scanning, quality check prompts, and integration with order data. Because of this, SFC can handle a large volume of orders daily (over 500,000 parcels handled per day in their facilities) while maintaining quality standards. Automation and software help reduce human errors – for example, the WMS might prevent an order from being marked complete until all items are scanned and verified. This use of technology is a key way SFC keeps quality high even as scale grows.High Picking and Packing Accuracy
SFC’s fulfillment process is designed for accuracy. They claim a >99.98% picking and packing accuracy rate with <0.003% discrepancy. These numbers indicate that out of, say, 100,000 orders, only a handful might have any issue – a performance that is world-class in logistics. How do they achieve this? SFC uses a refined and automated pick/pack process: workers likely use scanners to pick items (confirming each pick), and weight checks or visual inspections to ensure the packed order is correct. SFC’s warehouse management system, as noted, uses a mix of weight assessments and barcode verification to double-check orders in real time. For example, if an order is supposed to have 3 items and after packing, the weight is off by a certain margin, the system might flag it for a recount.The combination of human diligence and system oversight greatly reduces errors. SFC also trains its staff thoroughly in these procedures, ensuring everyone knows the importance of QC. For clients of SFC, this means when an order is placed, they can trust that the right items will be picked, properly packed, and sent out without mistake.
Returns Handling and Continuous QC
Another way SFC supports quality is by handling returns and feedback loops. If a customer return does happen, SFC can process that return at their warehouse – checking if the item is resellable or if there was a defect. They then update the inventory and report back any quality issues. Over time, this helps sellers identify if there’s a manufacturing issue or packaging problem. SFC’s role here is to be the eyes and hands that maintain quality after delivery too. By examining returned products and customer feedback, they can help the business improve product QC at the source. Moreover, SFC provides detailed reports and dashboards (like showing breakdowns of picking, storage, shipping, etc.). These analytics can highlight if errors are happening and at what stage, enabling continuous improvement. Essentially, SFC not only does QC, but also gives businesses transparency into the whole fulfillment process – a critical factor for maintaining quality in the long run.Certifications and Experience
It’s also worth noting that SFC has over 10 years of 3PL experience and is a recommended logistics provider for major platforms. They likely adhere to international quality standards (possibly ISO certification for warehouses, though not explicitly stated on their site). Their long track record and large scale (100,000+ merchants served) means their QC processes have been tested and refined over time. They understand common pitfalls in warehousing and have built processes to avoid them. For instance, being recognized by Amazon and Walmart platforms suggests they meet the strict accuracy and service level requirements those marketplaces demand. So, when you use SFC, you’re tapping into a matured system of quality control.6. Conclusion
In today’s hyper-competitive market, warehouse quality control isn’t optional—it’s existential. From avoiding costly recalls to nurturing customer loyalty, QC is the silent engine driving supply chain success. By choosing partners like SFC, businesses don’t just outsource storage; they invest in peace of mind.7. FAQs
Q1: What’s the difference between quality assurance (QA) and quality control (QC)?
A: QA focuses on preventing defects through process design, while QC involves detecting defects in existing products.Q2: How often should QC checks happen?
A: It varies. High-value items may need 100% inspection, while others use random sampling (e.g., 10% of batches).Q3: Can small businesses benefit from QC warehouses?
A: Absolutely! QC scales to any size, preventing errors that could cripple smaller budgets.Q4: Does QC slow down order fulfillment?
A: Not with modern tools. Automated systems like barcode scanners add seconds per check, avoiding delays.Q5: How do I measure QC effectiveness?
A: Track metrics like defect rate, return rate, and inspection pass/fail ratios over time.
Copyright statement: The copyright of this article belongs to the original author. Please indicate the source for reprinting.
Previous Post
Understanding Days Sales in Inventory(DSI), Definition, Formula, and More
Next Post
TikTok Shop Brazil: Strategic Expansion, Challenges, and Opportunities for Sellers
TAGS
Hot Research
Get a Custom China Fulfillment Solution with FREE Storage for 30 Days
Want to know about our services, fees or receive a custom quote?
Please fill out the form on the right and we will get back to you within a business day.
The more information you provide, the better our initial response
will be.