Table of Contents
What Is Fill Rate and How to Calculate It
Time: Aug 01,2024 Author: SFC Source: www.sendfromchina.com
Understanding fill rate is crucial for any business looking to optimize its supply chain. Fill rate measures the effectiveness of your order fulfillment process and has a direct impact on customer satisfaction.Our blog article offers an in-depth exploration of fill rate, including its definition, calculation, and strategies to enhance it, helping your business deliver superior service and achieve better performance.
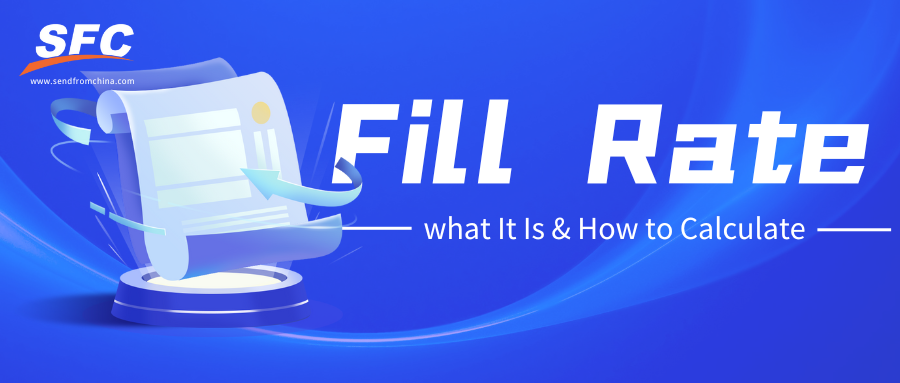
1. What Is Fill Rate
In supply chain management, fill rate is a critical metric that quantifies the efficiency and effectiveness of order fulfillment processes. Essentially, fill rate measures the percentage of customer orders that are met completely and on time from available stock, reflecting the ability of a company to meet customer demand without backordering or stockouts. High fill rates indicate robust inventory management and a smooth supply chain, which are crucial for maintaining customer satisfaction and loyalty.2. Why You Need to Calculate Fill Rate
Fill rate is not just a metric; it is a reflection of a company's operational health. A high fill rate ensures that customers receive what they need when they need it, directly impacting customer satisfaction and repeat business. Conversely, a low fill rate can lead to missed sales opportunities, decreased customer trust, and ultimately, a negative impact on the bottom line. Here are some reasons why your need to calculate fill rate:Enhancing Customer Satisfaction
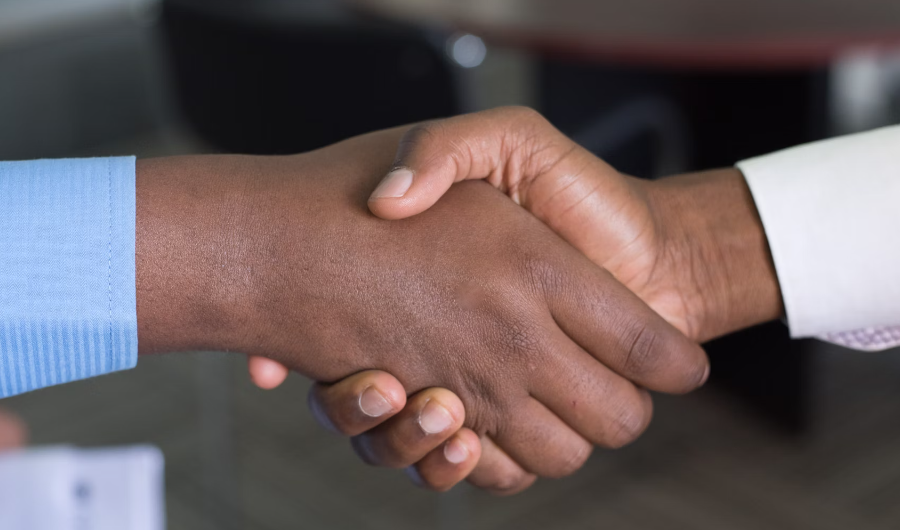
Improving Inventory Management
Fill rate provides insights into inventory performance, helping businesses identify and rectify inefficiencies. This ensures optimal inventory levels, reduces holding costs, and minimizes the risk of stockouts or overstocking.Boosting Operational Efficiency
A high fill rate indicates efficient supply chain operations. By regularly monitoring and improving fill rate, businesses can streamline processes, reduce lead times, and enhance overall operational efficiency.Gaining Competitive Advantage
In a competitive market, a superior fill rate can differentiate a company from its competitors. Businesses that consistently meet or exceed customer expectations are more likely to retain customers and attract new ones.3. What Are the Types of Fill Rate
Here are the main types of fill rate:Order Fill Rate
Order fill rate is the percentage of customer orders that are completely fulfilled from stock at hand. This type of fill rate focuses on the ability to meet entire orders rather than just individual items.Line Fill Rate
Line fill rate measures the percentage of order lines (distinct items in an order) that are completely fulfilled. This metric helps businesses understand the performance of specific product lines and identify potential issues in product availability.Unit Fill Rate
Unit fill rate is the percentage of individual units ordered that are fulfilled. It provides a granular view of inventory performance and is useful for pinpointing specific items that may be causing fulfillment problems.Case Fill Rate
Case fill rate is particularly relevant in wholesale and distribution. It measures the percentage of cases ordered by customers that are fully supplied. The metric is vital for businesses that deal with bulk orders and need to ensure that large quantities are managed efficiently.4. How to Calculate Fill Rate
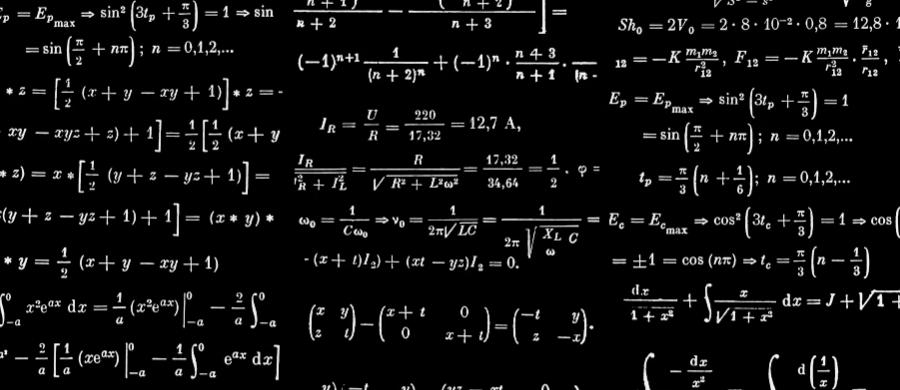
Fill Rate Formula
Fill Rate(%)=(Number of Units Delivered on Time/Total Number of Units Ordered)×100Example Calculation
For instance, if a customer orders 100 units of a product, and the company successfully delivers 90 units on time, the fill rate would be: Fill Rate(%)=(90/100)×100Calculating Different Types of Fill Rates
- Order Fill Rate: If a customer places 10 orders and 8 are fulfilled completely, the order fill rate is 80%.- Line Fill Rate: If there are 50 order lines and 45 are fulfilled, the line fill rate is 90%.
- Unit Fill Rate: If 1000 units are ordered and 950 are delivered, the unit fill rate is 95%.
- Case Fill Rate: If 200 cases are ordered and 180 are delivered, the case fill rate is 90%.
5. How to Define a Healthy Fill Rate
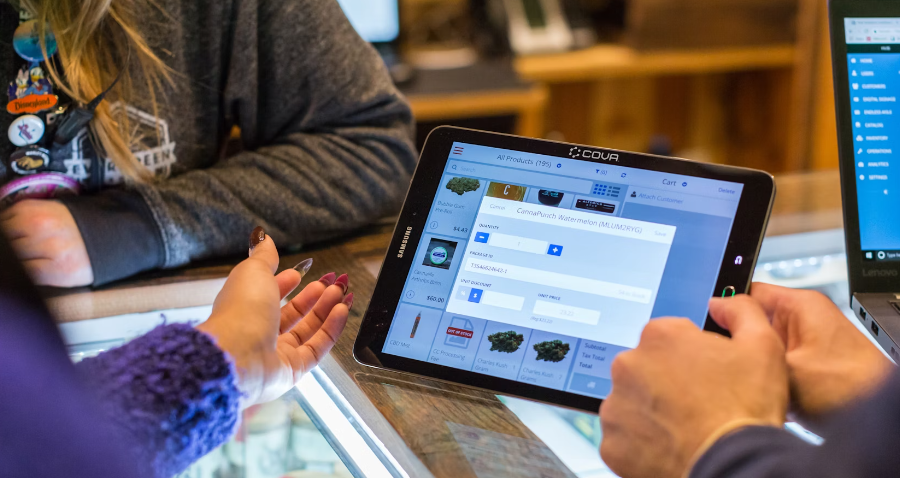
Aligning with Business Goals
Each business should define its healthy fill rate based on its unique goals, customer expectations, and operational capabilities. Setting realistic targets that align with overall business objectives is crucial for sustainable success.Regular Monitoring and Adjustment
Continuous monitoring of fill rate and adjusting strategies as necessary ensures that businesses can maintain a healthy fill rate. It involves regular audits, performance reviews, and adapting to changing market conditions.6. Challenges to Maintain a Healthy Fill Rate
.jpg)
Supply Chain Disruptions
Unpredictable supply chain disruptions, such as natural disasters, political instability, or global pandemics, can severely impact supply chain operations, making it challenging to maintain a healthy fill rate.Inaccurate Demand Forecasting
Inaccurate demand forecasting can lead to either overstocking or stockouts, both of which negatively affect fill rate. Investing in robust forecasting tools and methodologies is essential to mitigate this risk.Supplier Reliability
Dependence on unreliable suppliers can lead to delays and shortages, impacting the fill rate. Building strong relationships with reliable suppliers and diversifying the supplier base can help mitigate this risk.Inventory Management Issues
Poor inventory management practices, such as inadequate stock control, lack of visibility, and inefficient warehousing, can lead to fulfillment challenges. Implementing advanced inventory management systems can help address these issues.7. How to Improve Fill Rate
Enhancing Demand Forecasting
Investing in sophisticated demand forecasting tools and techniques can significantly improve fill rate. Accurate forecasts enable better inventory planning and reduce the likelihood of stockouts.Strengthening Supplier Relationships
Building strong relationships with reliable suppliers ensures a consistent supply of goods, minimizing disruptions. Regular communication and collaboration with suppliers can lead to better performance and reliability.Implementing Advanced Inventory Management Systems
Adopting advanced inventory management systems provides real-time visibility into stock levels, helping businesses manage inventory more effectively. Automated replenishment and stock control processes can also improve fill rate.Optimizing Warehouse Operations
Efficient warehouse operations, including proper warehouse layout design, streamlined picking and packing processes, and effective use of technology, can enhance fulfillment speed and accuracy, positively impacting fill rate.Continuous Process Improvement
Regularly reviewing and improving fulfillment processes ensures that businesses can adapt to changing conditions and maintain a high fill rate. Implementing lean methodologies and continuous improvement practices can drive operational excellence.8. Get Started with SFC Services
SFC stands at the forefront of order fulfillment with cutting-edge facilities in Shenzhen, China. Utilizing sophisticated software, we specialize in seamless and trustworthy fulfillment solutions for ecommerce, dropshipping, and crowdfunding platforms. At SFC, we are dedicated to accelerating your business growth through secure warehousing, efficient processing, customizable packaging options, and adaptable shipping strategies while saving you time and money.Whether you have or do not have a fulfillment partner, particularly your products manufactured in China, you should consider SFC. Click the button below and get help from SFC logistics experts.
What Makes SFC Special
Over 17 Years of 3PL and Order Fulfillment ExperienceAll-in-one Tracking Number
Popular Platform API Integration
30 Days of Free Storage
No Hidden Fee
Custom Packaging
Worldwide shipping solutions
Value-added Services
9. FAQs about Fill Rate
What is a good fill rate for retail?
A good fill rate for retail typically ranges between 95% to 99%, as customers expect prompt and complete order fulfillment. Higher fill rates are often necessary to maintain customer satisfaction and competitiveness.How does fill rate affect customer satisfaction?
Fill rate directly impacts customer satisfaction by ensuring that orders are fulfilled completely and on time. A high fill rate leads to happy customers, repeat business, and positive word-of-mouth, while a low fill rate can result in dissatisfied customers and lost sales.What tools can help improve fill rate?
Several tools can help improve fill rate, including demand forecasting software, advanced inventory management systems, warehouse management systems, and supply chain analytics platforms. These tools provide better visibility and control over the supply chain, leading to improved performance.How often should businesses review their fill rate?
Businesses should review their fill rate regularly, ideally on a monthly basis. Regular reviews help identify trends, spot potential issues early, and make necessary adjustments to maintain a high fill rate.Can a fill rate be too high?
While a high fill rate is generally positive, excessively high fill rates (close to 100%) may indicate overstocking, leading to increased holding costs and potential waste. It is important to balance fill rate with cost efficiency and overall supply chain performance.
Copyright statement: The copyright of this article belongs to the original author. Please indicate the source for reprinting.
Previous Post
What Is Supply Chain Management(SCM): All You Need to Know
Next Post
7 Small Tips to Create Custom Packaging for Your eCommerce Business
TAGS
Hot Research
Recent News
Get a Custom China Fulfillment Solution with FREE Storage for 60 Days
Want to know about our services, fees or receive a custom quote?
Please fill out the form on the right and we will get back to you within a business day.
The more information you provide, the better our initial response
will be.