Table of Contents
What Is Warehouse Efficiency and How To Improve It
Time: Dec 28,2023 Author: SFC Source: www.sendfromchina.com
In modern e-commerce, warehousing is not just a place to store inventory, but a crucial part of the supply chain. It plays an important role in receiving inventory, inventory management, picking & packing, fulfillment process, and shipping out. Therefore, the success of your business is subject to your warehouse efficiency.
But what is warehouse efficiency and how to improve it? Let's go through this blog article, you will have a deep understanding of these questions.
.png)
1. What Is Warehouse Efficiency
2. Why Warehouse Efficiency Is Important
Firstly, it significantly reduces operational costs. Efficient warehousing means optimizing storage space, streamlining inventory management, and enhancing order processing speed and accuracy.
This optimization leads to lower labor costs, reduced waste, and minimized losses from damaged or misplaced inventory. Cost-effective warehouse operations directly impact the bottom line, allowing businesses to maintain competitive pricing and improve profitability.
Secondly, warehouse efficiency is essential for customer satisfaction and retention. In today's fast-paced market, customers expect quick and reliable delivery of their orders. An efficient warehouse ensures that products are readily available, orders are fulfilled accurately, and shipping is expedited.
The reliability not only enhances the customer experience but also builds brand loyalty and reputation.
Inefficient warehousing can lead to delayed shipments, incorrect orders, and ultimately, dissatisfied customers, harming the business's long-term success.
3. How An Inefficient Warehouse Damages Your Business
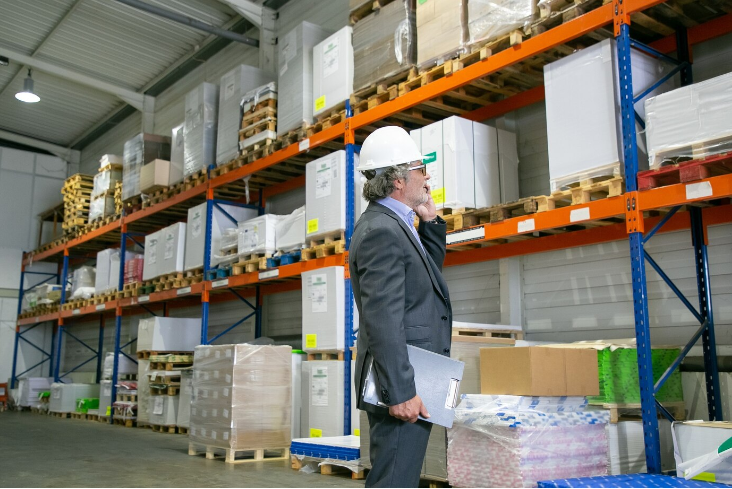
Firstly, it leads to increased operational costs due to poor space utilization, wasteful inventory practices, and inefficient labor deployment.
This inefficiency often results in higher overheads, with resources being spent on unnecessary storage, excessive manpower, and rectifying errors. The increased costs can erode profit margins and make the business less competitive in terms of pricing and investment in growth opportunities.
Secondly, an inefficient warehouse adversely impacts customer satisfaction and retention. Delays in order processing, errors in shipments, and frequent stockouts due to poor inventory management can lead to customer dissatisfaction.
In the age of e-commerce and fast-paced retail, customers expect quick and accurate deliveries. Failing to meet these expectations can result in lost sales, negative reviews, and a tarnished brand reputation.
Over time, these issues can lead to a significant loss of market share, as customers turn to competitors who can provide more reliable service.
4. How To Know the Efficiency of Your Warehouse
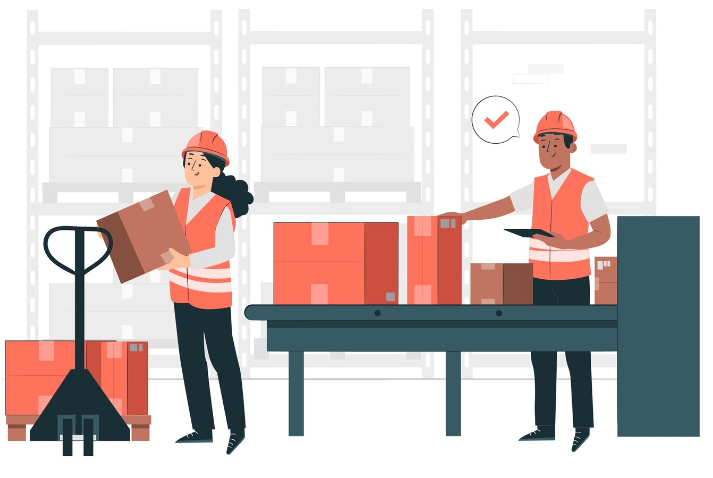
4.1 Inventory Accuracy
4.2 Order Accuracy
4.3 Turnover Rate
4.4 Space Utilization
4.5 Labor Productivity
4.6 Order Cycle Time
4.7 Customer Feedback
4.8 Technology and Automation
4.9 Cost Per Order
5. How To Improve Warehouse Efficiency
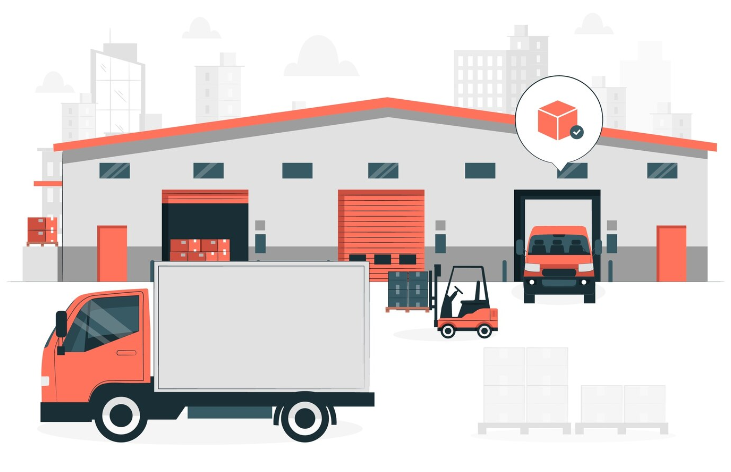
5.1 Optimize Warehouse Layout
This not only speeds up the order-picking process but also reduces worker fatigue and the likelihood of errors.
Additionally, a well-planned layout can maximize the use of available space, allowing for better organization and storage of inventory. This optimal use of space can prevent overcrowding and disorganization, which often leads to delays in locating and moving items.
5.2 Improve Inventory Management
This optimization reduces the space and resources required to store excess inventory, thereby lowering storage costs and minimizing the risk of product obsolescence or spoilage.
A well-managed inventory system allows for accurate tracking and easy retrieval of items, streamlining the picking and packing processes. This reduces the time spent by staff searching for products, leading to faster order fulfillment and increased productivity.
5.3 Warehouse Automation
This reduces the time and labor required for tasks like picking, packing, and sorting, leading to faster order fulfillment and reduced labor costs.
Automated systems are also more accurate than manual processes, minimizing errors in picking and inventory management, which in turn reduces the time and resources spent on correcting these errors.
5.4 Employee Training
Proper training ensures that workers understand the best practices and safety protocols, which minimizes the risk of accidents and errors.
This not only leads to a safer work environment but also reduces downtime caused by injuries or mistakes. Trained employees are better equipped to utilize warehouse technologies and systems effectively, ensuring that these tools are used to their full potential to optimize operations.
5.5 WMS (Warehouse Management System)
WMS enhances accuracy in inventory management, reducing the likelihood of overstocking or stockouts and ensuring timely replenishment of goods.
With real-time data and analytics, a WMS enables better forecasting and decision-making, allowing for more efficient use of resources and space. The automation of routine tasks, such as order picking and stock allocation, minimizes manual errors and speeds up operations, leading to faster order fulfillment and increased productivity.
5.6 Making KPIs List
KPIs such as order accuracy, inventory turnover rate, and average order fulfillment time offer quantifiable benchmarks that help in monitoring and assessing the performance of warehouse activities.
By regularly tracking these indicators, management can identify areas where the warehouse is performing well and areas that require improvement. This data-driven approach enables targeted interventions to address specific inefficiencies, leading to overall operational enhancements.
5.7 Taking Advantage of Technology
For instance, automation in picking and sorting significantly reduces the time and labor involved in these tasks, leading to quicker order fulfillment and reduced human error.
Technologies like RFID and barcode scanning improve inventory tracking and management, ensuring accurate stock levels and efficient retrieval of items. This precision in inventory control minimizes instances of overstocking or stockouts, facilitating smooth operations.
6. Get Start with SFC Order Fulfillment Service
1. Over 17 years 3PL and order fulfillment experience
2. DDP (Delivered Duty Paid) Service
3. All-in-one tracking number
4. API
5. 30 days of free storage
6. No hidden fee
7. Custom packaging
8. Worldwide shipping solutions
7. FAQs
1. What are the first steps to take in improving warehouse efficiency?
2. How can small warehouses compete with larger ones in terms of efficiency?
3. What are the most cost-effective technologies for improving warehouse efficiency?
4. How does workforce training impact warehouse efficiency?
5. Are there any quick wins in warehouse efficiency, or is it all about long-term strategies?

Copyright statement: The copyright of this article belongs to the original author. Please indicate the source for reprinting.
Previous Post
On-Time Delivery: All You Need To Know
Next Post
Order Fulfillment: Why Shipment Visibility Is Important For E-commerce
TAGS
Hot Research
Get a Custom China Fulfillment Solution with FREE Storage for 60 Days
Want to know about our services, fees or receive a custom quote?
Please fill out the form on the right and we will get back to you within a business day.
The more information you provide, the better our initial response
will be.