Table of Contents
Warehouse Receiving: Everything You Need To Kown
Time: May 14,2024 Author: SFC Source: www.sendfromchina.com
Warehouse receiving is a critical component of the supply chain, acting as the first checkpoint for goods entering a facility. The efficiency and accuracy of receiving processes can significantly impact inventory management, customer satisfaction, and overall operational success.
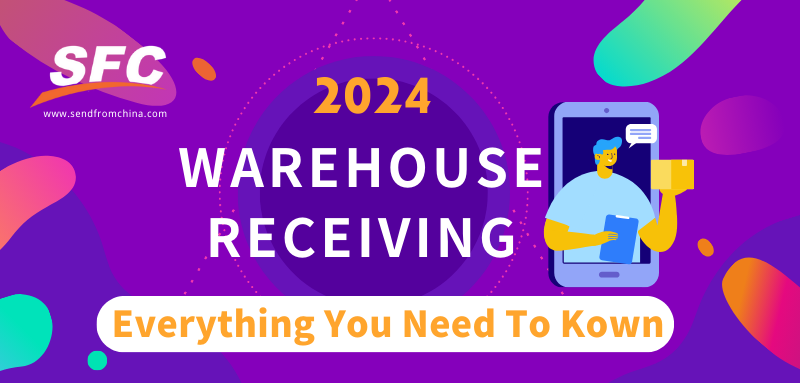
Content Table
1. What Is Warehouse Receiving
2. The Processes of Warehouse Receiving
3. Common Challenges in Warehouse Receiving
4. How to Improve Warehouse Receiving
5. FAQs
1. What Is Warehouse Receiving
Warehouse receiving is the process that starts when goods arrive at a warehouse and involves their inspection, documentation, and storage. This critical first step in inventory management ensures that items are accurately delivered and stored, setting the stage for efficient warehouse operations. Errors during this phase can lead to inventory inaccuracies, operational delays, and increased costs.
2. The Processes of the Warehouse Receiving
Warehouse receiving involves much more than just accepting inventory deliveries; it requires a series of crucial steps to verify both the accuracy and quantity of items received and ensure they are correctly stored. This complex process is vital for maintaining operational efficiency and avoiding costly mistakes. Below is a detailed overview of the standard procedures involved in receiving goods.
1. Arrival and Unloading
- Preparation: Before a shipment arrives, ensure that the docking area is clear and staff are prepared with the necessary equipment, such as forklifts, pallet jacks, and docking plates.
- Efficient Unloading: Use scheduled appointments to manage the flow of incoming trucks and avoid congestion at the dock. As trucks arrive, unload goods promptly while ensuring that handling does not damage the items.
2. Check-In
- Verification: As goods are unloaded, verify each item against the shipping manifest or delivery note. Check for correct quantities and reference numbers to ensure that what was ordered matches what was delivered.
- Organize for Inspection: Sort items based on type and priority for inspection, separating any that require special handling or immediate attention.
3. Inspection
- Quality Checks: Perform a thorough inspection of each item for quality and condition. Check for damages, defects, or inconsistencies. Use checklists to maintain consistency in how inspection criteria are applied.
- Handling Discrepancies: Immediately flag any discrepancies or issues discovered during inspection. This includes missing items, excess goods, or damaged products. Such issues should be documented with photographs if possible and reported to the supplier and inventory management team.
4. Documentation
- Recording Data: Accurately record all relevant data such as item numbers, descriptions, quantities received, condition of goods, and discrepancy notes. This documentation should be digital wherever possible to reduce errors and improve accessibility.
- Updating Systems: Enter all data into your Warehouse Management System (WMS) or relevant inventory management software. This step is crucial for maintaining accurate inventory records and facilitating efficient inventory control.
5. Labeling and Storing
- Labeling for Traceability: Apply labels that include critical information such as product codes, receiving date, and any special storage instructions. This ensures that items can be easily tracked throughout their lifecycle in the warehouse.
- Strategic Storing: Move items to their designated storage areas. Use zone picking or other organizational strategies to optimize the storage based on item type, frequency of access, and compatibility with other stored goods.
6. Integration into Inventory
- System Sync: Ensure that all information in the physical inventory matches the data entered into inventory management systems. This synchronization must be checked to avoid future discrepancies.
- Ready for Fulfillment: Once items are properly stored and records are updated, they should be flagged as available for order fulfillment in the system, completing the receiving process.
3. Common Challenges in Warehouse Receiving
Handling a warehouse receiving area can be fraught with challenges:
High Volume of Shipments
A high volume of shipments presents significant challenges in warehouse receiving primarily due to the increased complexity and potential for errors in handling large quantities of goods. It can overwhelm existing processes, leading to bottlenecks in unloading, inspection, and documentation. With more products to process, there's a greater risk of inventory mismanagement, such as misplacement or incorrect logging of items, which can disrupt inventory accuracy and overall operational efficiency.Inconsistent Supplier Deliveries
Inconsistent supplier deliveries pose a challenge in warehouse receiving because they disrupt planned inventory and resource management. When suppliers do not deliver goods on a consistent schedule or if the quantity and quality of shipments vary, it complicates the receiving process. It unpredictability can lead to staffing issues, storage complications, and a lack of necessary materials for production or sales. Ultimately, it affects the efficiency of the entire supply chain, requiring warehouses to adapt quickly to avoid shipping delays and maintain operational continuity.
Documentation Discrepancies
Documentation discrepancies are a significant challenge in warehouse receiving as they can lead to a variety of operational problems. When the paperwork such as shipping manifests, purchase orders, or delivery receipts contains errors or doesn't match the actual shipments, it can result in incorrect stock levels being recorded, delays in processing the inventory, and potential issues with order fulfillment. Ensuring accuracy in documentation is critical for maintaining an efficient supply chain and reducing the likelihood of costly errors.
Human Errors
ocumentation discrepancies are a challenge in warehouse receiving because they can cause significant disruptions. When the documentation such as invoices, purchase orders, or shipping manifests does not accurately reflect the goods received, it leads to errors in inventory records. It can cause delays in the warehouse workflow, affect stock levels and order fulfillment accuracy, and complicate audits and compliance. Ensuring accurate and consistent documentation is critical for smooth operations and reliable inventory management.
4. How to Improve Warehouse Receiving
To enhance warehouse receiving, several detailed measures can be implemented:Implement a Warehouse Management System (WMS)
Deploying a WMS can drastically improve inventory tracking and data accuracy by automating the entry and update of goods as they arrive and are processed. Implementing a WMS reduces human error and speeds up the entire receiving process.Regular Staff Training
Consistent training programs are essential to ensure that warehouse staff are proficient in the latest inventory management techniques and technologies. Regular staff training includes training on how to handle goods, use new software, and apply best practices for accuracy.Thorough Inspection Protocols
Thorough inspection protocols are key to enhancing warehouse receiving efficiency. They allow for immediate verification of goods against quality standards and order specifications, ensuring any discrepancies or damages are detected early. This practice not only maintains inventory accuracy but also supports customer satisfaction by preventing defective or incorrect products from entering the supply chain. Ultimately, rigorous inspections reduce the likelihood of costly returns and reinforce overall operational effectiveness.Frequent Audits
Frequent audits are a vital method to improve warehouse receiving as they help maintain ongoing accuracy and integrity of the inventory records. Regular audits enable early detection and correction of errors that might occur during the receiving process, such as miscounts or misplacements. It ensures that inventory levels are consistently accurate, supporting efficient warehouse operations and reliable supply chain management. By regularly verifying the data against physical stock, warehouses can improve operational decisions and reduce discrepancies, leading to better overall efficiency.Document Double-Checking
Double-checking documents in warehouse receiving is crucial because it ensures the accuracy of the paperwork associated with shipments, such as delivery notes, purchase orders, and invoices. It helps prevent administrative errors that could lead to discrepancies between what has been ordered and what is received. By verifying documents meticulously, warehouses can ensure correct stock levels and order fulfillment, improve financial accuracy, and reduce the potential for costly inventory or shipping errors.5. FAQs
1. What is the most critical step in the warehouse receiving process?
Inventory verification is crucial as it ensures the accuracy of what was ordered versus what was delivered.2. How can technology improve the receiving process?
Technology, like a Warehouse Management System (WMS), can streamline operations by automating inventory tracking and reducing errors.3. What are some common mistakes made during warehouse receiving?
Common mistakes include miscounting items, overlooking damaged goods, and incorrect documentation.4. How often should inventory be audited within the warehouse?
Inventory should be audited regularly, typically quarterly or biannually, depending on the volume and turnover rate.5. What training should staff undergo to improve receiving efficiency?
Staff should receive training in inventory management systems, proper unloading and inspection techniques, and accurate record-keeping.
Copyright statement: The copyright of this article belongs to the original author. Please indicate the source for reprinting.
Previous Post
What Are The Pros And Cons Of Crowdfunding
Next Post
TAGS
Hot Research
Get a Custom China Fulfillment Solution with FREE Storage for 30 Days
Want to know about our services, fees or receive a custom quote?
Please fill out the form on the right and we will get back to you within a business day.
The more information you provide, the better our initial response
will be.