Table of Contents
Warehouse Traceability: What It Is & Why It Matters for Ecommece
Time: Feb 19,2025 Author: SFC Source: www.sendfromchina.com
Warehouse traceability plays a pivotal role in the efficiency and reliability of ecommerce businesses. As ecommerce continues to grow, ensuring smooth operations from product storage to delivery becomes increasingly crucial. At its core, warehouse traceability refers to the ability to track products within the supply chain, from their arrival at the warehouse to their final dispatch to customers.In today’s competitive ecommerce landscape, maintaining control over inventory and ensuring quick, error-free order fulfillment are critical for retaining customers and building brand loyalty. In this article, we explore what warehouse traceability is, how it enhances ecommerce operations, and why it is essential for success.
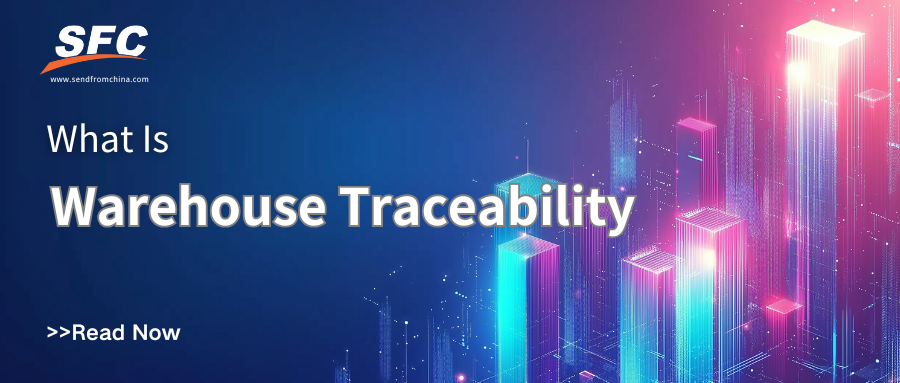
1. What Is Warehouse Traceability
Warehouse traceability refers to the process of tracking goods and products within a warehouse. It allows businesses to monitor the movement of items from receiving through to picking, packing, and dispatching. With traceability, every stage of a product's journey within the warehouse is logged, ensuring real-time visibility and control over inventory.Warehouse traceability is facilitated through a combination of technologies, such as barcodes, RFID (radio-frequency identification), and Warehouse Management Systems (WMS), that automate data collection and provide detailed insights into the location and status of every product.
Why Warehouse Traceability Important for Ecommerce
For ecommerce businesses, warehouse traceability enhances efficiency, reduces errors, and fosters a more seamless customer experience. Traceability ensures that businesses can track inventory in real-time, which helps reduce stockouts, avoid overstocking, and ultimately meet customer demands more effectively.Moreover, it contributes to greater operational transparency, helping businesses optimize supply chain management while ensuring compliance with regulations.
2. Processes of Warehouse Traceability
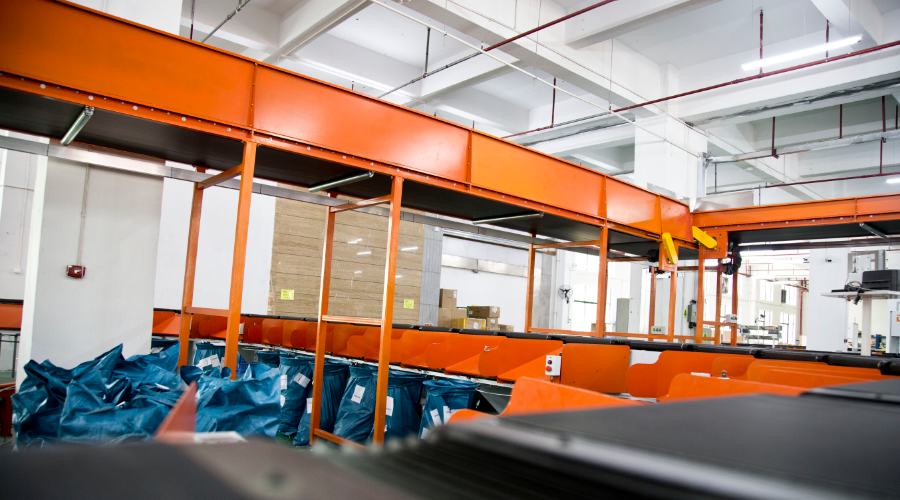
Inventory Tracking
One of the main processes in warehouse traceability is the continuous tracking of inventory. It involves logging every product as it enters and moves through the warehouse. Using advanced inventory management software, ecommerce businesses can automate the tracking process, minimizing human error and ensuring real-time updates. By recording product movements and updating stock levels, businesses gain immediate insight into inventory availability, preventing stockouts and overstock situations.Barcode Scanning and RFID
Barcode scanning and RFID are two powerful technologies that enhance warehouse traceability. Barcodes are the most common method used to identify products in a warehouse, while RFID technology allows for automatic identification without direct line-of-sight scanning.Both technologies ensure that each item can be traced from its point of entry into the warehouse to its final destination. Barcode scanners and RFID readers are used to capture product information, automatically logging each item’s movement and ensuring that data remains accurate and up to date.
Real-Time Data Integration
A crucial aspect of modern warehouse traceability is real-time data integration. When product data is captured, it should be instantly updated in the central warehouse management system. It ensures that all stakeholders, from warehouse staff to business managers, have access to the latest information regarding inventory levels, order statuses, and shipment tracking. The integration of real-time data with ecommerce platforms ensures smoother operations and more efficient order fulfillment.here’s how these processes work together as a product moves from warehouse receiving to customer delivery:
1. Receiving inventory: When a shipment arrives at the warehouse, each product is scanned by a barcode or RFID reader, and the WMS updates the system with the item’s quantity and its storage location.
2. Storing inventory: The WMS directs staff to the optimal storage location. Once the item is shelved, it is scanned again to update its location in the inventory system.
3. Order placement: When a customer places an order, the WMS locates the item and reserves it, ensuring it isn’t oversold.
4. Picking and packing: Using a picking list created by the WMS, warehouse staff scan every item during both picking and packing to ensure the order is accurate and complete.
5. Shipping: After packing and labeling, a final scan updates the system to indicate that the item has left the warehouse. The customer is provided with tracking details linked to their shipment.
6. Returns processing: If an item is returned, it’s scanned during receipt and inspection. After restocking, the WMS updates the inventory levels to keep the data accurate.
3. Benefits of Warehouse Traceability for Ecommerce
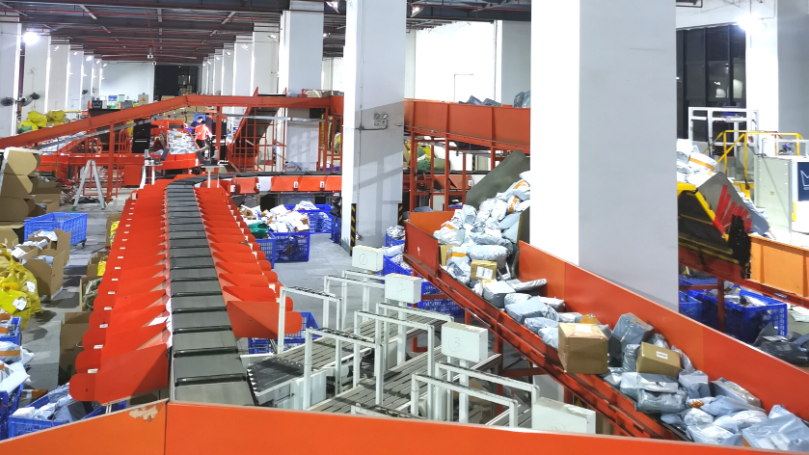
Enhanced Inventory Management
With warehouse traceability, ecommerce businesses can achieve more precise inventory management. Real-time tracking and visibility of stock levels allow businesses to forecast demand more accurately, streamline order fulfillment processes, and reduce instances of stockouts. Effective inventory management ensures that products are always available when customers place an order, improving overall business operations.Improved Order Fulfillment
The ability to track inventory and monitor order processing throughout the warehouse ensures that products are picked, packed, and shipped quickly and efficiently. By knowing the exact location of products at any given moment, ecommerce businesses can minimize delays and avoid errors during the order fulfillment process, leading to quicker deliveries and more satisfied customers.Better Customer Experience
Customer satisfaction is directly tied to order accuracy and delivery speed. With a traceable warehouse system in place, customers can track their orders in real-time, providing transparency and reassurance. Furthermore, traceability helps prevent mistakes, ensuring that customers receive the right products at the right time. The ability to guarantee fast, reliable delivery ultimately boosts customer loyalty.Regulatory Compliance
Certain industries require businesses to maintain strict records of their inventory for compliance with regulations. Warehouse traceability allows ecommerce companies to track products for compliance with safety, quality, and regulatory standards. It is particularly important for sectors like pharmaceuticals, food, and electronics, where traceability ensures product integrity and regulatory adherence.4. How to Implement Warehouse Traceability
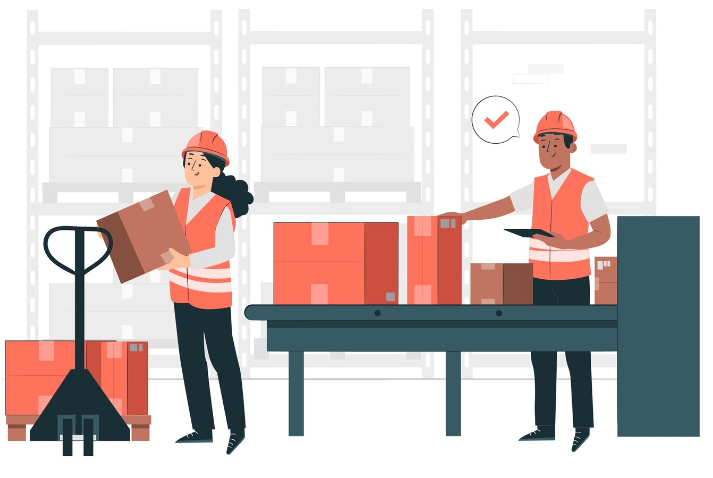
Choosing the Right Traceability Tools
The first step in implementing warehouse traceability is selecting the right tools and technologies. The choice will depend on the specific needs of your ecommerce business. For example, businesses with high-order volumes may benefit from RFID technology, while smaller businesses may find barcode systems more cost-effective.Integrating Systems and Processes
Once the right tools are in place, the next step is integrating them with your existing warehouse management systems and operational processes. Ensuring smooth integration between your traceability tools and WMS is crucial for real-time data syncing and efficient warehouse operations.5. Conclusion
In today’s fast-paced ecommerce environment, warehouse traceability plays a pivotal role in optimizing operations, improving inventory management, and enhancing customer satisfaction. By implementing technologies such as barcode scanning and RFID, automating data collection, and integrating real-time tracking systems, businesses can maintain better control over their supply chain and ensure timely, accurate deliveries. Warehouse traceability is not just a tool for increasing operational efficiency but also a critical element in delivering a seamless and reliable customer experience.6. FAQs
1. How does warehouse traceability help in managing inventory?
Warehouse traceability helps businesses track inventory in real time, allowing for accurate stock levels and reducing the risk of stockouts or overstocking. It ensures that inventory is always available when needed and optimizes inventory management processes.2. What are the main technologies used in warehouse traceability?
The two main technologies used are barcode scanning and Radio Frequency Identification (RFID). Both enable efficient tracking of products, providing visibility into inventory movement and ensuring accurate data capture.3. Can warehouse traceability improve customer service?
Yes, warehouse traceability allows businesses to track orders in real time, ensuring fast and accurate deliveries. Customers benefit from increased transparency and fewer errors, resulting in higher satisfaction and loyalty.4. What industries benefit the most from warehouse traceability?
Industries like pharmaceuticals, food, electronics, and any sector that requires strict regulatory compliance benefit greatly from warehouse traceability. These industries rely on accurate records for safety, quality assurance, and regulatory standards.5. How can warehouse traceability help with compliance?
Warehouse traceability ensures that businesses can maintain accurate records of product movements, making it easier to comply with industry regulations. Whether it's for safety standards, product recalls, or quality assurance, having traceable inventory is crucial for maintaining compliance.
Copyright statement: The copyright of this article belongs to the original author. Please indicate the source for reprinting.
Previous Post
Shipping Options for Your Ecommerce Business
Next Post
TAGS
Hot Research
Get a Custom China Fulfillment Solution with FREE Storage for 30 Days
Want to know about our services, fees or receive a custom quote?
Please fill out the form on the right and we will get back to you within a business day.
The more information you provide, the better our initial response
will be.