Table of Contents
What Consists of Fulfillment Costs? A Detailed Guide
Time: Oct 21,2024 Author: SFC Source: www.sendfromchina.com
Fulfillment costs are an unavoidable part of running an e-commerce business, but understanding and optimizing fulfillment costs can make a huge difference in your bottom line. From warehousing to picking, packing, and shipping, each aspect of the fulfillment process comes with its own expenses.In this guide, we’ll explain how to calculate fulfillment costs, explore factors that influence them, and share practical tips for reducing these expenses. By taking control of your fulfillment operations, you’ll improve both cost-efficiency and customer experience.
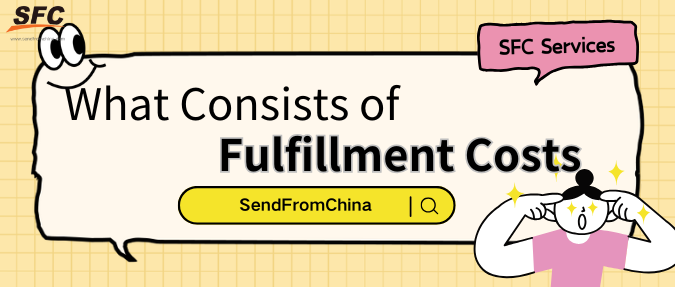
1. Understanding Order Fulfillment
Order fulfillment is a critical aspect of any e-commerce or retail business. It involves a series of steps from when an order is placed online to when the customer receives the product. These steps include inventory management, picking and packing, shipping, and even managing returns. While it might seem straightforward, fulfilling orders efficiently and cost-effectively can significantly impact a business’s profitability.For businesses to remain competitive, especially with the growing demand for faster and more reliable delivery options, understanding what consists of fulfillment costs is crucial. These costs can accumulate across different stages of the fulfillment process, making it essential for companies to track, calculate, and manage these expenses effectively.
2. How to Calculate Fulfillment Costs
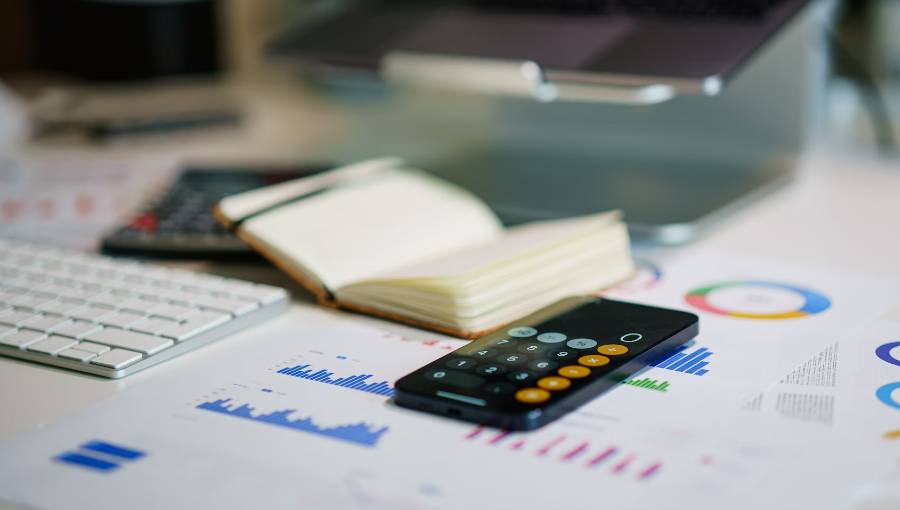
Receiving Costs: These are the costs associated with receiving goods into the warehouse or fulfillment center. It includes unloading trucks, checking inventory, and storing goods.
Storage Costs: The costs for keeping inventory in a warehouse until an order is placed. These costs are typically calculated based on space used (in square footage or cubic meters) and the duration for which products are stored.
Picking and Packing Costs: These are labor and material costs incurred when selecting products from storage (picking) and preparing them for shipment (packing). Efficiency in this area can lead to substantial cost reductions.
Shipping Costs: The fees charged for transporting the order from the fulfillment center to the customer. It is often influenced by the destination, weight of the package, and the shipping speed chosen.
Return Handling Costs: If a customer returns an item, the business bears the cost of processing the return, restocking the item, and, in some cases, refunding the customer. Return processing costs must be factored into the overall fulfillment costs.
Packaging Materials: Packaging materials include the boxes, bubble wrap, or other materials required to safely pack and ship products. Depending on the fragility or size of the product, this can add significant costs.
3. Factors Affecting Fulfillment Costs
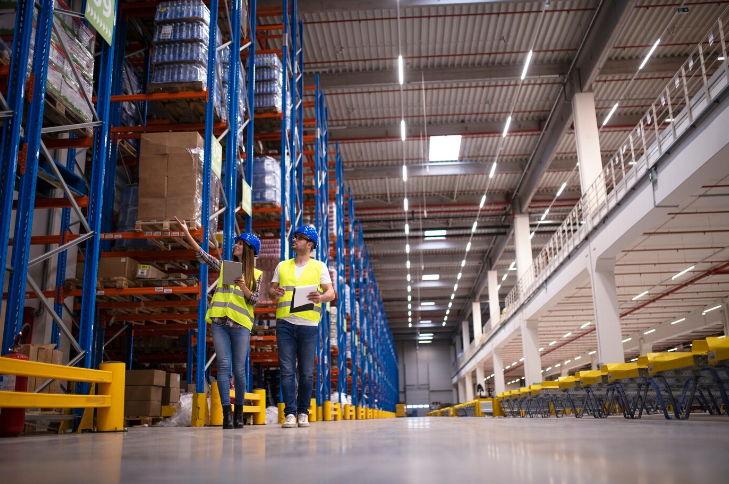
Order Volume and Size
The number of orders processed daily and the size or weight of the products being shipped significantly impact fulfillment costs. High order volumes typically mean more time spent on picking, packing, and shipping. Larger or heavier items tend to incur higher shipping fees.Businesses that experience fluctuations in order volume, such as seasonal surges, must account for variable labor costs and possible storage overflow fees during peak times.
Storage Requirements
The amount of inventory stored and its duration in the warehouse affects the overall storage costs. Fast-moving items that don’t spend much time in storage can help minimize costs, whereas slow-moving items occupying warehouse space for extended periods may increase storage fees.Additionally, products that require specialized storage environments (e.g., climate control, hazardous material handling) can come with premium storage fees.
Geographical Location
Where your fulfillment centers are located can greatly influence your shipping costs. Fulfillment centers positioned closer to your customer base can reduce transit times and shipping fees. Conversely, businesses with a geographically dispersed customer base may face higher costs to ship products across longer distances.International orders also introduce complexities with customs, duties, and tariffs that can inflate shipping costs.
Packaging Material and Labor
Efficient packing minimizes waste and reduces the cost of shipping. However, packaging requirements can vary based on product type. Fragile items need more protective materials, adding to both packaging and labor costs. Labor-intensive products that require careful handling or assembly can drive up labor costs associated with fulfillment.4. How to Reduce Fulfillment Costs
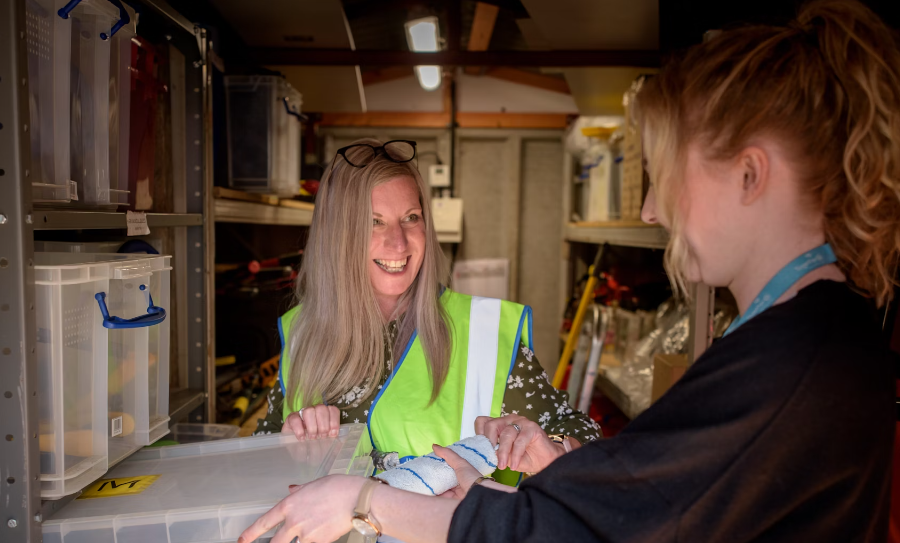
Optimizing Warehouse Operations
Improving warehouse layout and organization can significantly reduce the time required for picking and packing, ultimately lowering labor costs. Implementing strategies like zone picking, where products are grouped by type or popularity, can streamline the order fulfillment process.Additionally, investing in inventory management systems can help businesses track inventory levels accurately, preventing overstocking or stockouts that lead to increased storage costs.
Automating Fulfillment Processes
Automation can significantly reduce labor costs by handling repetitive tasks such as sorting, packing, and labeling. Automated systems, such as conveyor belts, robotic picking systems, and automated packaging machines, help speed up the fulfillment process and reduce errors.Though the initial investment in automation technology can be high, the long-term savings on labor and increased efficiency typically outweigh the costs.
Leveraging Volume Discounts
Many carriers offer discounted shipping rates for high-volume businesses. By consolidating shipments or negotiating with multiple carriers, businesses can secure lower shipping fees. Similarly, ordering packaging materials in bulk can reduce per-unit packaging costs.Working with 3PLs that have established relationships with carriers can also lead to better shipping rates for small to medium-sized businesses.
Outsourcing to Third-party Logistics (3PL) Providers
Outsourcing fulfillment to 3PL providers can be a cost-effective solution for businesses looking to scale. 3PL providers often have the infrastructure, expertise, and partnerships necessary to fulfill orders more efficiently than an in-house operation. Additionally, they offer flexible storage options and shipping solutions, allowing businesses to scale up or down based on demand.5. Common Third-party Logistics Fulfillment Costs Model
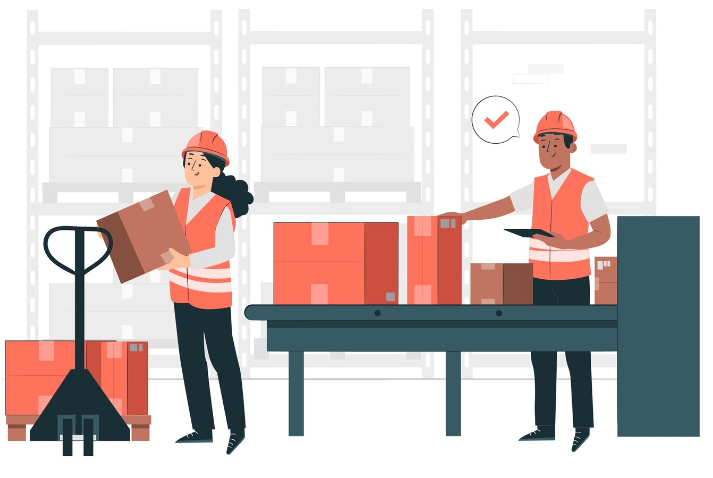
Receiving Fees: This covers the cost of receiving inventory from manufacturers or suppliers, typically charged on a per pallet or per unit basis.
Storage Fees: Most 3PLs charge for storage based on the amount of warehouse space your products occupy, calculated by pallet, shelf, or cubic meter.
Pick and Pack Fees: These fees are usually based on the number of items picked and packed per order. Some 3PLs charge a flat rate, while others have tiered pricing based on order volume.
Shipping Fees: 3PLs pass along shipping fees charged by the carriers they use. They may also offer discounted rates due to their volume-based contracts with shipping carriers.
Kitting and Assembly Fees: For products that require bundling or assembly before shipping, additional kitting fees may apply. These services can vary greatly depending on the complexity of the task.
Returns Processing Fees: If the 3PL provider handles returns on your behalf, they will charge a fee for receiving, inspecting, and restocking returned items.
6. How SFC Services Can Help
SFC stands at the forefront of order fulfillment with cutting-edge facilities in Shenzhen, China. Utilizing sophisticated software, we specialize in seamless and trustworthy fulfillment solutions for ecommerce, dropshipping, and crowdfunding platforms. At SFC, we are dedicated to accelerating your business growth through secure warehousing, efficient processing, customizable packaging options, and adaptable shipping strategies while saving you time and money.Whether you have or do not have a fulfillment partner, particularly your products manufactured in China, you should consider SFC. Click the button below and get help from SFC logistics experts.
What Makes SFC Special
Over 17 Years of 3PL and Order Fulfillment ExperienceAll-in-one Tracking Number
Popular Platform API Integration
30 Days of Free Storage
No Hidden Fee
Custom Packaging
Worldwide shipping solutions
Value-added Services
7. FAQs
1. What are the most common fulfillment costs?
The most common fulfillment costs include storage fees, picking and packing fees, shipping fees, and return handling costs. Additional costs may include receiving fees and packaging material expenses.2. How can I reduce fulfillment costs for my e-commerce business?
To reduce fulfillment costs, consider optimizing warehouse operations, automating the fulfillment process, leveraging volume discounts from shipping carriers, and outsourcing fulfillment to third-party logistics providers.3. How does order volume affect fulfillment costs?
Higher order volumes typically increase fulfillment costs due to the additional labor and packaging materials required. However, businesses with large volumes may be able to negotiate discounted rates with carriers or third-party logistics providers.4. Is outsourcing to a 3PL provider cost-effective?
Outsourcing to a 3PL provider can be cost-effective, particularly for businesses looking to scale without investing in their own infrastructure. However, it's important to compare providers to ensure they offer transparent pricing and the services you need.5. What is the difference between fulfillment and shipping costs?
Fulfillment costs cover the entire process of preparing an order for shipment, including picking, packing, and storage. Shipping costs are the fees charged by carriers to transport the order from the fulfillment center to the customer.
Copyright statement: The copyright of this article belongs to the original author. Please indicate the source for reprinting.
Previous Post
What Are the Differences Between Dropshipping and Wholesale
Next Post
TAGS
Hot Research
Recent News
- Third Party Logistics Definition, Process, and Advantages
- What Is Ecommerce Fulfillment? The Definition, Process, and Benefits
- Where Does Shein Ship From
- What Does Order Fulfilled Mean? A Complete Guide for Online Shoppers
- Amazon FBA Packaging Requirements 2025: A Seller’s Guide to Compliance and Success
Get a Custom China Fulfillment Solution with FREE Storage for 60 Days
Want to know about our services, fees or receive a custom quote?
Please fill out the form on the right and we will get back to you within a business day.
The more information you provide, the better our initial response
will be.