Table of Contents
Why Order Accuracy Matters in Order Fulfillment
Time: Oct 18,2024 Author: SFC Source: www.sendfromchina.com
As customer expectations for speed and precision continue to rise, order accuracy has become critical to fulfillment success. Fulfilling orders with 100% accuracy is key to reducing costly mistakes and improving customer retention.This article will guide you through the essentials of order accuracy, show why it matters for your business, and offer tips on how to fine-tune your processes for better results.
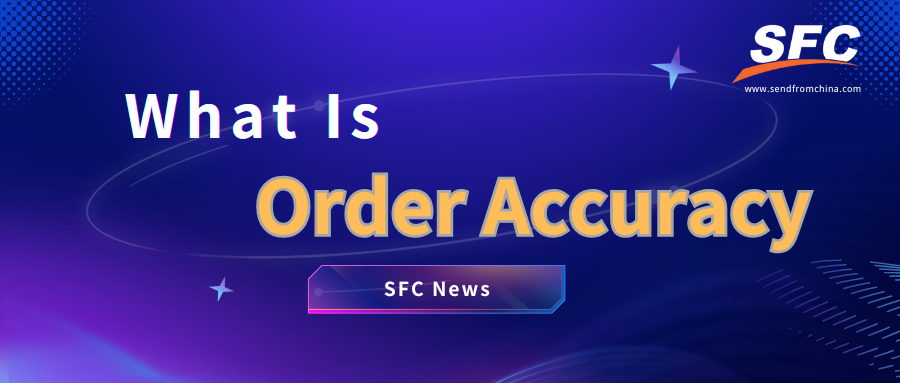
1. What Is Order Accuracy
Order accuracy refers to the precision and correctness with which a customer's order is processed, packed, and delivered. It encompasses all steps in the fulfillment process—starting from inventory management, picking, and packing to shipping. Order accuracy measures the ability to ensure that the right items, in the correct quantities, reach the right customers, in the expected condition, within the promised time frame.Maintaining high order accuracy means minimizing or eliminating errors such as incorrect products, wrong quantities, and even packaging mistakes. Accurate orders are critical to customer satisfaction and business success, ensuring smooth and profitable operations.
2. Why Order Accuracy Matters
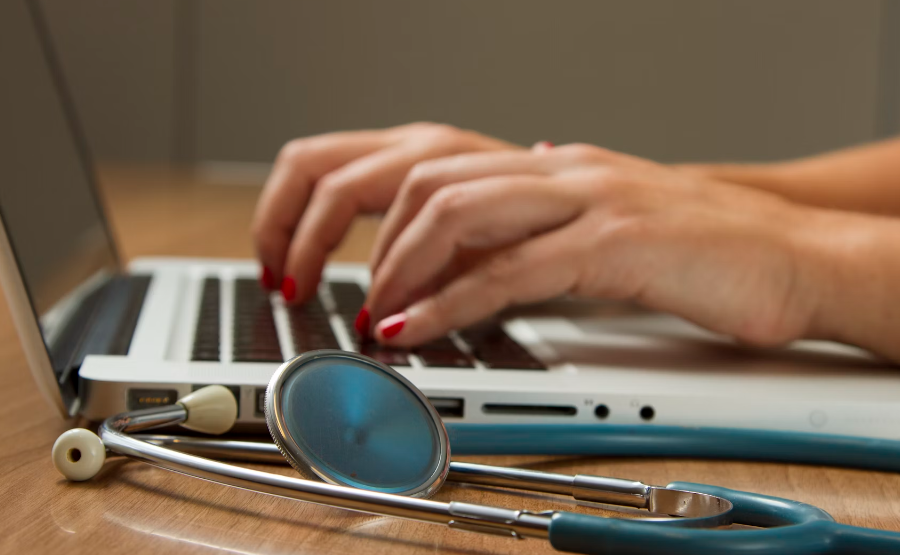
Customer Satisfaction and Loyalty
An accurate order is foundational for keeping customers happy. If a customer receives the wrong item, the wrong size, or a damaged product, it can negatively impact their experience. Consistently accurate orders lead to higher customer satisfaction, promoting repeat purchases and fostering brand loyalty.Reduced Returns and Refunds
High order accuracy reduces the number of returns and refunds that businesses must process. Returns are costly and time-consuming, adding an extra burden to both customers and the fulfillment team. By ensuring accurate orders, companies can minimize the need for returns and the associated costs.Lower Operational Costs
Errors in orders lead to increased costs in terms of returns processing, reshipping, and customer service handling. By improving order accuracy, businesses can save significant amounts of money that would otherwise be wasted on correcting mistakes.Positive Brand Image
A reputation for delivering accurate and on-time orders strengthens a company’s brand. On the other hand, frequent mistakes damage trust, leading to negative reviews and a decline in customer retention.Streamlined Operations
Accurate order fulfillment ensures that the entire logistics and supply chain operates efficiently. A higher order accuracy rate means fewer bottlenecks, better workflow, and smoother warehouse operations, all of which contribute to overall business efficiency.3. How to Measure Order Accuracy
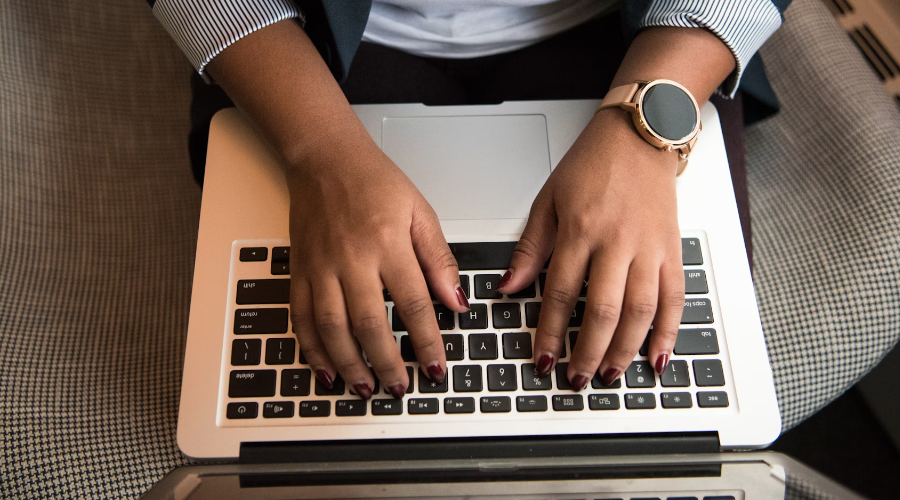
Order Accuracy Rate
The primary metric for measuring order accuracy is the order accuracy rate. This simple yet effective metric reflects the percentage of orders that are fulfilled without errors. The formula is:Order Accuracy Rate = (Number of Error-Free Orders / Total Orders Processed) × 100
Tracking this percentage over time helps businesses identify trends, track performance, and make necessary adjustments to their processes.
Inventory Accuracy Rate
Another related metric is inventory accuracy, which measures the degree to which the physical inventory matches the recorded inventory levels. Inaccurate inventory counts can lead to fulfillment errors, so maintaining accurate inventory records is critical.Perfect Order Rate
A broader metric to consider is the "perfect order rate." This KPI measures the percentage of orders that are shipped on time, without any damage, errors, or discrepancies. A high perfect order rate signals that your fulfillment process is working efficiently.Customer Complaints Related to Order Accuracy
Tracking customer complaints related to order accuracy can provide additional insight. Analyzing these complaints helps pinpoint areas of the process that may need improvement.Root Cause Analysis for Errors
When errors do occur, it’s essential to conduct a root cause analysis to determine why the error happened. Was it a picking error, an issue with inventory management, or a packaging mistake? Understanding the root cause enables businesses to address these issues and prevent them from happening in the future.4. Key Factors Affecting Order Accuracy
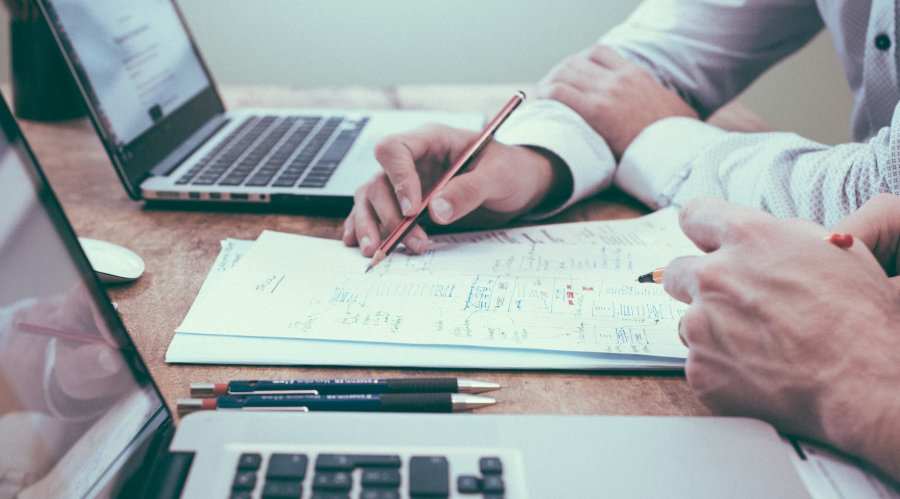
Inventory Management Systems
Having an accurate, real-time inventory management system is fundamental to preventing errors. A well-maintained inventory management system allows warehouse staff to pick the right items based on accurate stock levels. Inaccurate inventory data can lead to out-of-stock situations or incorrect picking.Warehouse Layout and Organization
The physical layout and organization of a warehouse can directly affect how quickly and accurately orders are fulfilled. Poorly organized warehouses can lead to picking errors, as staff may struggle to locate the correct items. A well-structured warehouse with clear labeling and optimized slotting can significantly enhance order accuracy.Picking and Packing Processes
Errors during picking and packing are common sources of order inaccuracies. Implementing strict quality control processes during these stages is essential. For example, barcode scanning can be used to verify that the correct items are being picked and packed.Employee Training
Well-trained employees are more likely to perform their tasks accurately and efficiently. Regular training on fulfillment procedures, use of technology, and best practices are key to maintaining high order accuracy.Technology and Automation
Utilizing technology such as barcode scanners, automated picking systems, and order management software can drastically reduce human errors. Automation helps speed up fulfillment processes while minimizing the chances of mistakes.5. Tips to Improve Order Accuracy
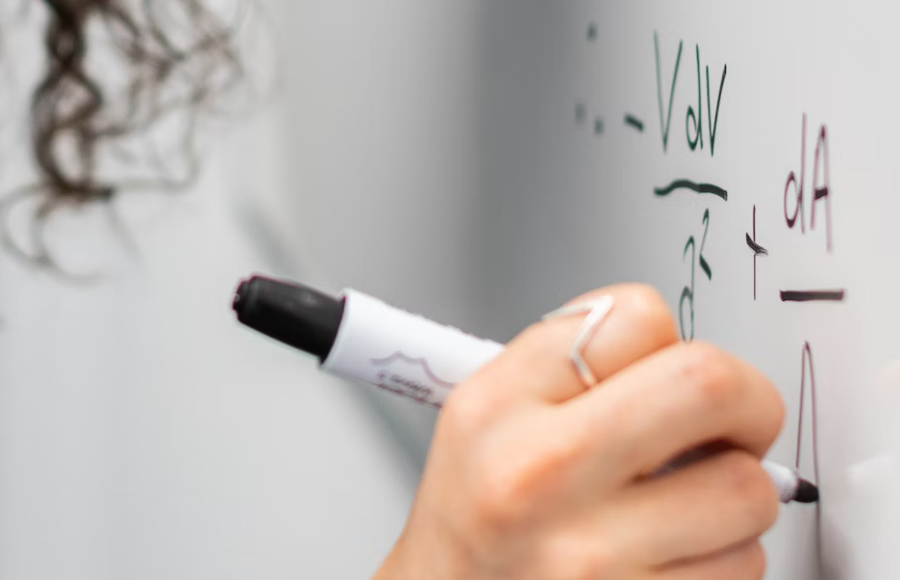
Implement Quality Control Checks
Quality control (QC) checks at different stages of the fulfillment process help catch errors before they reach customers. Implementing a final quality control check before shipping ensures that orders are accurate.Leverage Automation
Automating key parts of the fulfillment process, such as inventory management, order picking, and packing, can help eliminate human errors. Automated systems ensure consistency and accuracy across all orders.Utilize Barcode Scanning
Barcode scanning is an effective way to verify that the correct items are picked and packed. Integrating barcode technology into your warehouse processes helps to significantly reduce picking errors.Regularly Audit Inventory
Conducting regular inventory audits ensures that stock levels are accurate and up-to-date. Discrepancies between physical stock and inventory records often lead to errors in order fulfillment, so frequent auditing helps mitigate this risk.Enhance Employee Training Programs
Investing in regular training for your fulfillment team helps ensure that employees understand the importance of order accuracy and know how to avoid mistakes. Training should cover everything from correct picking and packing procedures to using technology tools effectively.Monitor Key Performance Indicators (KPIs)
Regularly tracking key performance indicators such as order accuracy rate, perfect order rate, and inventory accuracy helps identify areas for improvement. Use these KPIs to set benchmarks and continuously optimize your fulfillment process.6. How SFC Services Can Help
SFC stands at the forefront of order fulfillment with cutting-edge facilities in Shenzhen, China. Utilizing sophisticated software, we specialize in seamless and trustworthy fulfillment solutions for ecommerce, dropshipping, and crowdfunding platforms. At SFC, we are dedicated to accelerating your business growth through secure warehousing, efficient processing, customizable packaging options, and adaptable shipping strategies while saving you time and money.Whether you have or do not have a fulfillment partner, particularly your products manufactured in China, you should consider SFC. Click the button below and get help from SFC logistics experts.
What Makes SFC Special
Over 17 Years of 3PL and Order Fulfillment ExperienceAll-in-one Tracking Number
Popular Platform API Integration
30 Days of Free Storage
No Hidden Fee
Custom Packaging
Worldwide shipping solutions
Value-added Services
7. FAQs
1. What is a good order accuracy rate?
A good order accuracy rate is generally considered to be 97% or higher. However, striving for 100% is ideal to minimize costly errors and maximize customer satisfaction.2. What are common causes of order inaccuracies?
Common causes of order inaccuracies include human errors during picking and packing, outdated or incorrect inventory data, poor warehouse organization, and lack of proper employee training.3. How does order accuracy impact customer retention?
Order accuracy has a direct impact on customer retention. Customers who receive accurate, on-time orders are more likely to make repeat purchases and remain loyal to a brand. In contrast, frequent errors can lead to lost customers and negative reviews.4. Can technology improve order accuracy?
Yes, technology plays a critical role in improving order accuracy. Tools such as barcode scanning, automated picking systems, and order management software can significantly reduce human errors and streamline the fulfillment process.5. How can I reduce order errors in my warehouse?
To reduce order errors, implement quality control checks, leverage automation, regularly audit your inventory, enhance employee training, and optimize your warehouse slotting practices.
Copyright statement: The copyright of this article belongs to the original author. Please indicate the source for reprinting.
Previous Post
What Consists of Fulfillment Costs? A Detailed Guide
Next Post
TAGS
Hot Research
Recent News
Get a Custom China Fulfillment Solution with FREE Storage for 60 Days
Want to know about our services, fees or receive a custom quote?
Please fill out the form on the right and we will get back to you within a business day.
The more information you provide, the better our initial response
will be.